Introduzione
La pressatura isostaticaè un processo produttivo che offre numerosi vantaggi e applicazioni in vari settori. Consiste nel sottoporre un materiale a una pressione uguale in tutte le direzioni per ottenere densità e forma uniformi. Questo metodo è particolarmente vantaggioso rispetto ad altre tecniche di produzione. La pressatura isostatica consente di produrre pezzi con forme interne complesse e pareti lunghe e sottili, che potrebbero non essere facilmente ottenibili con altri metodi. Tuttavia, è importante considerare i limiti della pressatura isostatica, come la minore precisione delle superfici pressate e i tassi di produzione inferiori rispetto alle tecniche alternative.
Indice dei contenuti
- Introduzione
- Panoramica della pressatura isostatica
- Vantaggi della pressatura isostatica
- Svantaggi della pressatura isostatica
- Pressatura isostatica di sacchi a secco
- Pressatura isostatica di sacchi umidi
- Pressatura monoassiale e isostatica
- Preparazione della polvere per la pressatura isostatica
- Applicazioni della pressatura isostatica in sacchi umidi
- Applicazioni della pressatura isostatica con sacco a secco
- Conclusione
Panoramica della pressatura isostatica
Spiegazione della pressatura isostatica
La pressatura isostatica è una tecnica di lavorazione delle polveri che utilizza una pressione fluida per compattare le miscele di polveri e ridurre la porosità. La miscela di polveri viene incapsulata utilizzando la pressione isostatica, che applica una pressione uguale da tutte le direzioni. Questo processo prevede il confinamento della polvere metallica all'interno di una membrana flessibile o di un contenitore ermetico, creando una barriera di pressione tra la polvere e il mezzo di pressurizzazione (liquido o gas) che la circonda.
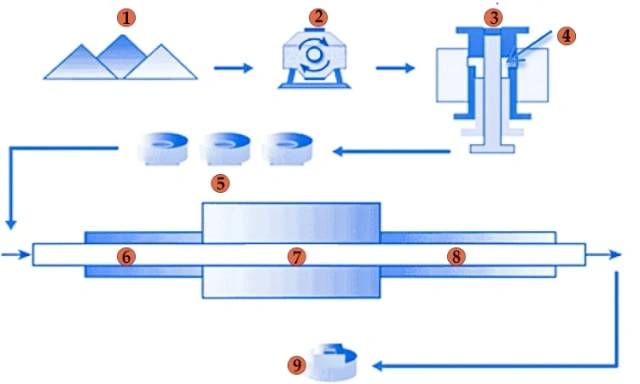
Tipi di pressatura isostatica: a sacco umido e a sacco asciutto
Esistono due tipi generali di pressatura isostatica: a sacco umido e a sacco asciutto. La variante a sacco umido prevede l'utilizzo di uno stampo elastomerico separato che viene caricato all'esterno della pressa e poi immerso nel recipiente di pressione. Dopo la pressurizzazione e la compattazione, lo stampo viene rimosso dal recipiente, il pezzo viene recuperato e il processo viene ripetuto. È possibile caricare più stampi nel recipiente per un singolo ciclo di pressurizzazione.
D'altra parte, la variante con sacchetto a secco elimina la fase di immersione creando uno stampo integrato nel recipiente di pressurizzazione. Nel processo con sacco a secco, la polvere viene aggiunta allo stampo, lo stampo viene sigillato, viene applicata la pressione e quindi il pezzo viene espulso. Lo stampo integrato in questo processo facilita l'automazione rispetto al processo a sacchi umidi.
Pressioni di formatura per la ceramica
La pressatura isostatica offre vantaggi unici per le applicazioni di ceramica e refrattari. Applica una forza uniforme e uguale su tutto il prodotto, indipendentemente dalla sua forma o dimensione. Questa caratteristica consente la formazione di forme di prodotto con tolleranze precise, riducendo la necessità di costose lavorazioni meccaniche. Il processo di pressatura isostatica è stato ampiamente utilizzato per la formazione di refrattari ad alta temperatura, ceramiche, carburi cementati, magneti permanenti al lantanio, materiali al carbonio e polveri di metalli rari.
La pressatura isostatica è diventata un valido strumento di produzione utilizzato in vari settori industriali per consolidare le polveri o eliminare i difetti nelle fusioni. La sua capacità di raggiungere alte densità compatte e di produrre forme complesse ne ha fatto una scelta privilegiata in molte applicazioni. Tuttavia, è importante notare che il costo degli utensili e la complessità del processo sono maggiori rispetto alla pressatura monoassiale.
Vantaggi della pressatura isostatica
La pressatura isostatica offre diversi vantaggi rispetto ad altri metodi di produzione. Vediamo nel dettaglio alcuni dei vantaggi della pressatura isostatica rispetto ad altre tecniche:
Vantaggi della pressatura isostatica rispetto ad altri metodi di produzione
- Bassa distorsione alla cottura: La pressatura isostatica comporta una distorsione minima durante il processo di cottura, garantendo l'accuratezza dimensionale del prodotto finale.
- Restringimento costante alla cottura: La contrazione dei pezzi pressati isostaticamente durante il processo di cottura è costante e porta a risultati prevedibili e uniformi.
- I pezzi possono essere cotti senza essiccazione: A differenza di altri metodi, la pressatura isostatica consente di cuocere i pezzi senza doverli essiccare preventivamente, risparmiando tempo ed energia.
- Sono possibili livelli inferiori di legante nella polvere: La pressatura isostatica consente di utilizzare livelli inferiori di legante nella miscela di polveri, riducendo la necessità di ulteriori fasi di lavorazione.
- La maggior parte dei compatti verdi (non cotti) può essere lavorata: I compatti verdi pressati isostaticamente possono essere facilmente lavorati, offrendo flessibilità nel processo di produzione.
- Basse tensioni interne nel compatto pressato: Il processo di pressatura isostatica determina basse tensioni interne nel pezzo compattato, riducendo il rischio di cricche o deformazioni.
- Capacità del pezzo pressato molto grande: La pressatura isostatica consente di produrre pezzi molto grandi con il metodo del sacco umido, ampliando la gamma di applicazioni.
- Basso costo degli utensili: La pressatura isostatica ha costi di attrezzaggio inferiori rispetto ad altri metodi di produzione, il che la rende un'opzione economicamente vantaggiosa per le piccole produzioni.
- Maggiore densità per una data pressione di pressatura: La pressatura isostatica consente di ottenere una densità maggiore per una data pressione di pressatura rispetto ai metodi di pressatura meccanica, ottenendo pezzi più resistenti e durevoli.
- Capacità di pressare compatti con un rapporto lunghezza-diametro molto elevato: La pressatura isostatica consente di produrre compatti con elevati rapporti lunghezza-diametro, rendendola adatta a un'ampia gamma di applicazioni.
- Capacità di pressare pezzi con forme interne: La pressatura isostatica può accogliere pezzi con forme interne, come filettature, scanalature, dentellature e rastremazioni, ampliando le possibilità di progettazione.
- Capacità di pressare pezzi lunghi e sottili: La pressatura isostatica è in grado di produrre pezzi lunghi a parete sottile, offrendo versatilità nella progettazione dei prodotti.
- Capacità di pressare polveri deboli: La pressatura isostatica può pressare efficacemente polveri deboli, migliorando l'utilizzo del materiale e la qualità complessiva del prodotto finale.
- Capacità di pressare un compatto con due o più strati di polvere con caratteristiche diverse: La pressatura isostatica consente di produrre compatti con più strati di polvere, ciascuno con caratteristiche diverse, migliorando le proprietà e le prestazioni del materiale.
La pressatura isostatica offre una serie di vantaggi che la rendono un metodo di produzione preferito in diversi settori. Esploriamo in dettaglio alcune delle sue capacità.
Capacità della pressatura isostatica
- Densità uniforme: La pressatura isostatica garantisce che il pezzo compattato abbia una densità uniforme, con conseguente ritiro costante durante la sinterizzazione o la pressatura isostatica a caldo e una deformazione minima.
- Flessibilità della forma: La pressatura isostatica consente di produrre forme e dimensioni difficili o impossibili da ottenere con altri metodi, offrendo flessibilità di progettazione.
- Dimensione dei componenti: La pressatura isostatica può adattarsi a un'ampia gamma di dimensioni dei componenti, dalle forme massicce da 30 tonnellate quasi nette della metallurgia delle polveri ai piccoli pezzi MIM che pesano meno di 100 grammi.
- Pezzi più grandi: Le dimensioni della camera di pressione isostatica sono l'unico limite alle dimensioni dei pezzi, il che la rende adatta alla produzione di componenti di grandi dimensioni.
- Possibilità di leghe migliorate: La pressatura isostatica consente di aumentare gli elementi di lega senza indurre segregazione nel materiale, ampliando le possibilità di scelta del materiale.
- Tempi di consegna ridotti: La pressatura isostatica consente di produrre in modo economico forme complesse dal prototipo alle quantità di produzione, riducendo significativamente i tempi di consegna rispetto ai metodi di produzione tradizionali.
- Riduzione dei costi di materiale e lavorazione: Con la pressatura isostatica si possono fabbricare pezzi di forma quasi netta, riducendo gli scarti di materiale e i costi di lavorazione.
La pressatura isostatica trova applicazione in diversi settori industriali, grazie ai suoi vantaggi e alle sue capacità uniche. Vediamo alcune applicazioni comuni della pressa isostatica.
Applicazioni della pressa isostatica
- Prodotti farmaceutici
- Esplosivi
- Prodotti chimici
- Prodotti alimentari
- Combustibile nucleare
- Ferriti
Altri settori di applicazione delle presse isostatiche (prodotti farmaceutici, esplosivi, prodotti chimici, ferriti per combustibili nucleari)
La pressatura isostatica è un metodo di produzione versatile che offre numerosi vantaggi rispetto ad altre tecniche. È applicabile a un'ampia gamma di materiali e può produrre forme e dimensioni complesse con elevata precisione. Che si tratti di ottenere una densità uniforme, di pressare pezzi con forme interne complesse o di ridurre i costi di attrezzaggio, la pressatura isostatica si rivela una valida opzione di produzione in molti settori.
Svantaggi della pressatura isostatica
La pressatura isostatica è un metodo di produzione che offre diversi vantaggi rispetto ad altre tecniche. Tuttavia, non è privo di svantaggi. Vediamo nel dettaglio alcuni degli svantaggi della pressatura isostatica:
Minore precisione delle superfici pressate
Uno svantaggio della pressatura isostatica è la minore precisione delle superfici pressate adiacenti al sacco flessibile. Ciò significa che può essere necessaria una lavorazione successiva per ottenere la precisione desiderata. In confronto, le tecniche di pressatura meccanica o di estrusione producono superfici pressate più precise.
Costi più elevati per le presse per sacchi a secco completamente automatiche
Le presse a secco completamente automatiche, comunemente utilizzate per la pressatura isostatica, richiedono una polvere essiccata a spruzzo relativamente costosa. Questo può aumentare il costo complessivo del processo. L'uso di materiali di alta qualità e di attrezzature specializzate contribuisce alle spese più elevate associate a questo tipo di pressa.
Tassi di produzione inferiori rispetto all'estrusione o alla compattazione con stampo
La pressatura isostatica tende ad avere tassi di produzione inferiori rispetto ai metodi di estrusione o compattazione con stampi. Ciò significa che il processo potrebbe non essere altrettanto efficiente in termini di volume di produzione. È importante considerare i requisiti di produzione e le tempistiche quando si sceglie tra le diverse tecniche di pressatura.
Nonostante questi svantaggi, la pressatura isostatica offre comunque vantaggi unici che la rendono un'opzione valida per alcune applicazioni. Consente una bassa distorsione e un ritiro costante durante la cottura, permette la lavorazione di compatti verdi e offre la possibilità di pressare pezzi con forme interne e alti rapporti lunghezza-diametro. Inoltre, la pressatura isostatica può raggiungere densità più elevate rispetto alla pressatura meccanica e consente di pressare compatti con più strati di polvere.
È importante valutare i pro e i contro della pressatura isostatica in relazione alle specifiche esigenze di produzione per determinare se è la scelta giusta per una particolare applicazione.
Pressatura isostatica in sacchi a secco
Spiegazione e applicazioni della pressatura isostatica con sacco a secco
La pressatura isostatica a sacchi a secco è un metodo per compattare i materiali in polvere in una massa solida e omogenea prima della lavorazione o della sinterizzazione. Si tratta di un processo semplice che produce billette o preforme ad alta integrità con distorsioni o cricche minime alla cottura. Questo processo è particolarmente adatto alla produzione di articoli in metallo duro relativamente piccoli con geometria assialsimmetrica.
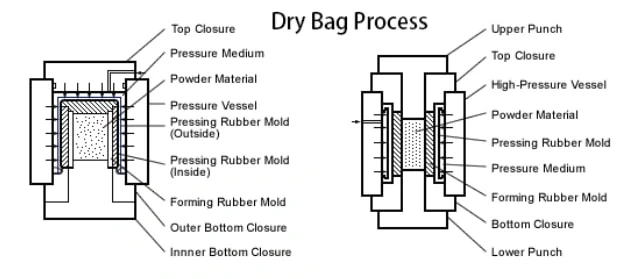
processo con sacco a secco
Vantaggi dell'automazione nella pressatura isostatica dei sacchi a secco
Il principale vantaggio delle presse a sacco a secco è la possibilità di automazione, che consente una produzione di massa o semi-massa economicamente vantaggiosa di articoli in metallo duro con geometria complessa. Si tratta di aste, tubi, boccole, sfere, pistoni, punte, viti, ugelli e altro ancora.
L'automazione della pressatura isostatica dei sacchi a secco consente anche la produzione di compatti verdi cavi di forma quasi netta con dimensioni esterne e interne precise. Ciò riduce significativamente la quantità di lavorazioni necessarie, con conseguente riduzione della produzione di trucioli.
Ruolo della qualità della polvere di WC-Co e della progettazione dello stampo di pressatura
La qualità della polvere di WC-Co e la progettazione dello stampo di pressatura giocano un ruolo cruciale nella fabbricazione efficace dei green compact in metallo duro. La qualità della polvere deve essere selezionata con cura per garantire una corretta compattazione e le proprietà desiderate nel prodotto finale.
Le diverse opzioni per la progettazione degli stampi di pressatura, come gli stampi integrati o intercambiabili, offrono flessibilità nel processo di pressatura. Gli stampi integrati sono preferibili quando le dimensioni degli articoli in carburo rimangono costanti per un certo periodo, mentre i sistemi di stampi flessibili sono più adatti a frequenti cambi di stampo.
Componenti delle presse per sacchi a secco
Le presse per sacchi a secco sono costituite da una pompa ad alta pressione, uno stampo di pressatura elastico, una camera di pressatura con una membrana e un recipiente di pressione. La pressione viene generata dalla pompa ad alta pressione e trasmessa allo stampo di pressatura riempito di polvere di WC-Co in modo radiale attraverso una membrana. Lo stampo di pressatura viene caricato manualmente o automaticamente.
Un ciclo di pressatura dura in genere 5-10 minuti e produce un compatto verde. I sistemi a sacchi a secco possono pressare aste o tubi con diametro fino a 200 mm e lunghezza fino a 600 mm. I diametri interni ed esterni di questi tubi possono essere pressati con tolleranze che vanno da 0,1 a 1 mm, a seconda delle loro dimensioni.
In conclusione, la pressatura isostatica a secco è un metodo efficiente per compattare i materiali in polvere in masse solide e omogenee. Offre vantaggi quali l'automazione per la produzione di grandi volumi, dimensioni precise e requisiti di lavorazione ridotti. La qualità della polvere di WC-Co e la progettazione degli stampi di pressatura sono fattori cruciali per ottenere una produzione di successo.
Pressatura isostatica in sacchi umidi
Spiegazione e applicazioni della pressatura isostatica a sacchetto umido
La tecnologia wet bag è un metodo di pressatura isostatica a freddo in cui la polvere viene riempita in uno stampo e sigillata ermeticamente all'esterno del recipiente in pressione. Lo stampo viene quindi immerso nel fluido in pressione all'interno del recipiente e la pressione isostatica viene applicata alla superficie esterna dello stampo, comprimendo la polvere in una massa solida.
Questo processo non è così comune come la pressatura isostatica dei sacchi a secco, ma esistono oltre 3.000 presse per sacchi a umido utilizzate in tutto il mondo. Le dimensioni dei sacchi umidi possono variare da 50 mm a 2000 mm di diametro.
La tecnologia dei sacchi umidi è relativamente lenta, con tempi di lavorazione che vanno dai 5 ai 30 minuti. Tuttavia, l'uso di pompe ad alto volume e di meccanismi di caricamento migliorati può contribuire a velocizzare il processo.
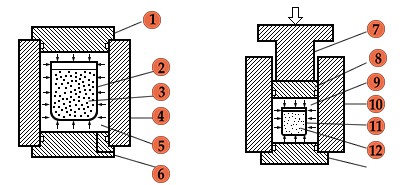
Processo Wet Bag (1.Chiusura superiore 2.Stampo in gomma 3.Polvere 4.Alta pressione 5.Mezzo di pressione 6.Chiusura inferiore 7.Stelo 8.Pistone 9.Mezzo di pressione 10.Vaso ad alta pressione 11.Stampo in gomma 12.Polvere 13.Chiusura inferiore)
Vantaggi della pressatura isostatica a sacco umido
-
La pressatura isostatica in sacchi umidi offre diversi vantaggi:
-
Densità uniforme: L'isopressatura a sacco umido può avvicinarsi al concetto teorico di pressatura isostatica, ottenendo un compatto con densità uniforme e basse tensioni intrappolate. Ciò consente la lavorazione allo stato verde senza distorsioni.
-
Distorsione ridotta: Quando vengono cotti, i pezzi prodotti con l'isopressatura a sacchi umidi non subiscono praticamente alcuna distorsione, riducendo o eliminando la necessità di costose lavorazioni.
Potenziale di automazione: L'isopressatura a sacchi umidi si presta bene all'automazione, rendendola adatta alla pressatura di serie relativamente lunghe di compatti ad alti ritmi di produzione.
Differenza tra isopressatura a sacco umido e a sacco secco
-
La differenza principale tra la pressatura isostatica a sacco umido e quella a sacco secco è il metodo di compattazione della polvere:
-
Isopressatura a sacco umido: Nella pressatura isostatica a sacco umido, la polvere viene compattata in uno stampo elastomerico sigillato e completamente immerso in un fluido pressurizzato. Questo metodo è utilizzato per la produzione di bassi volumi di pezzi speciali, per la prototipazione e per la ricerca e sviluppo.
Pressatura isostatica con sacco a secco: Nella pressatura isostatica a secco, lo stampo elastomerico è parte integrante della pressa isostatica. La pressione applicata è per lo più biassiale e il processo può essere automatizzato per la produzione di grandi volumi.
Sia la pressatura isostatica a sacco umido che quella a sacco secco presentano vantaggi e svantaggi. Il sacco umido è più adatto alla produzione di pezzi di grandi dimensioni e consente di ottenere densità più elevate con un attrito minimo. Tuttavia, le operazioni di carico e scarico degli stampi possono ridurre la produttività e limitare l'automazione. La pressatura isostatica con sacco a secco, invece, ha un vantaggio in termini di automazione e velocità di produzione.
In generale, la pressatura isostatica viene scelta per ottenere densità compatte elevate e per accedere a forme che non possono essere compattate con presse monoassiali. La scelta tra la pressatura isostatica a sacco umido e quella a sacco secco dipende dai requisiti specifici del processo produttivo.
Pressatura monoassiale e isostatica
Limitazioni della pressatura monoassiale che possono essere superate dalla pressatura isostatica
Alcune limitazioni della pressatura uniassiale che riguardano l'imballaggio regolare delle particelle possono essere superate dalla pressatura isostatica. La pressatura isostatica applica una pressione da tutte le direzioni, a differenza della pressatura monoassiale che applica una sola direzione. Ciò consente una compattazione più uniforme e una maggiore uniformità di imballaggio. La pressatura isostatica viene comunemente eseguita con due metodi: wet-bag e dry-bag.
Nella pressatura isostatica a sacco umido, la polvere viene riempita in uno stampo flessibile, sigillato e immerso in un liquido in un recipiente ad alta pressione. Il liquido viene pressurizzato e la pressione viene trasmessa alla polvere attraverso la parete flessibile dello stampo, provocandone la compattazione. La pressatura isostatica a sacchi umidi offre una maggiore uniformità di confezionamento rispetto alla pressatura uniassiale. È possibile utilizzare pressioni fino a 1000 GPa, anche se le unità di produzione più comuni operano fino a 200-300 MPa. La pressatura isostatica a sacchi umidi, abbinata alla lavorazione verde 3D, è utilizzata per fabbricare parti ceramiche complesse di altissima qualità.
La pressatura isostatica a secco è più facile da automatizzare rispetto al processo a umido. Si tratta di uno stampo in gomma strettamente collegato al recipiente di pressione. Tuttavia, il liquido pressurizzato non agisce da tutte le direzioni, quindi è necessaria un'attenta progettazione dello stampo per garantire un imballaggio omogeneo delle particelle nella polvere compatta.
Confronto tra corpi verdi prodotti da pressatura monoassiale e isostatica
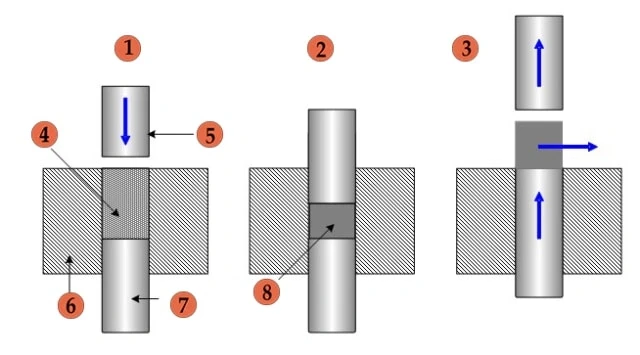
Illustrazione della tecnologia di pressatura uniassiale (1. Fase di riempimento dello stampo 2. Compattazione 3. Espulsione del pezzo 4. Polvere 5. Punzone superiore 6. Stampo 7. Punzone inferiore 8. Compatto "verde")
Se si confronta la pressatura monoassiale con quella isostatica, la pressatura monoassiale è più adatta per forme piccole ad alta velocità di produzione. Tuttavia, l'attrito delle pareti dello stampo può determinare densità non uniformi, soprattutto per rapporti d'aspetto elevati. La pressatura isostatica, invece, può essere utilizzata per forme piccole o grandi, semplici o complesse. La densità verde uniforme che fornisce offre una contrazione più uniforme durante la sinterizzazione, importante per il controllo della forma e l'uniformità delle proprietà. La pressatura isostatica elimina anche la necessità del legante ceroso utilizzato nella pressatura uniassiale, eliminando la necessità di operazioni di deceratura.
Per la pressatura isostatica si utilizzano utensili per elastomeri a basso costo, ma è possibile ottenere tolleranze strette solo per le superfici pressate contro un mandrino in acciaio altamente preciso. Le superfici a contatto con l'utensile in elastomero possono richiedere una post-lavorazione per ottenere tolleranze strette e buone finiture superficiali.
In sintesi, la pressatura isostatica supera alcune limitazioni della pressatura monoassiale applicando una pressione da tutte le direzioni. Offre una maggiore uniformità di impaccamento, una contrazione più uniforme durante la sinterizzazione ed elimina la necessità di un legante in cera. La pressatura isostatica può essere effettuata con metodi a sacco umido o a sacco asciutto, ciascuno con i propri vantaggi e limiti.
Preparazione della polvere per la pressatura isostatica
Requisiti della polvere per la pressatura isostatica
La pressatura isostatica è una tecnica di lavorazione della polvere che utilizza una pressione fluida per compattare un pezzo. Per ottenere risultati ottimali, è necessario soddisfare determinati requisiti per quanto riguarda la polvere utilizzata nella pressatura isostatica.
Un requisito importante è la distribuzione granulometrica della polvere. Per la pressatura isostatica, si consiglia di utilizzare polveri con granulometrie comprese tra 1 e 5 μm. Questo intervallo di dimensioni consente la formazione di materiali con densità superiori al 98% di quella teorica. L'uso di polveri di allumina non drogata con una dimensione media delle particelle di circa 0,5 μm è risultato efficace per ottenere queste densità.
Un altro requisito è il contenuto di legante nella miscela di polveri. Il legante serve a tenere insieme le particelle di polvere durante il processo di pressatura. Il contenuto specifico di legante dipende dal tipo di polvere utilizzata e dalle proprietà desiderate del prodotto finale. In genere, si utilizza un contenuto di legante del 20%-30%, con una miscela di cera di cellulosa come scelta comune.
Regolazioni della distribuzione granulometrica e del contenuto di legante
Per ottimizzare il condizionamento della polvere prima della pressatura isostatica, è possibile apportare modifiche alla distribuzione granulometrica e al contenuto di legante.
La distribuzione granulometrica può essere regolata macinando la polvere con una granulometria più fine. Idealmente, per la polvere utilizzata nella pressatura isostatica è auspicabile una granulometria inferiore a 75 μm. Questa granulometria più fine consente una migliore compattazione e garantisce un pellet più omogeneo.
Anche il contenuto di legante può essere regolato in base ai requisiti specifici del pezzo da produrre. Aumentando il contenuto di legante si può ottenere una maggiore resistenza del pellet pressato, mentre diminuendolo si può ottenere una struttura più porosa. È importante trovare il giusto equilibrio tra resistenza e porosità per ottenere le proprietà desiderate nel prodotto finale.
Considerando attentamente i requisiti della polvere nella pressatura isostatica e apportando modifiche alla distribuzione granulometrica e al contenuto di legante, i produttori possono produrre pezzi di alta qualità con le proprietà desiderate. La pressatura isostatica offre un metodo versatile ed efficace per la compattazione delle polveri, consentendo la produzione di un'ampia gamma di materiali.
ConclusioniIn conclusione, la pressatura isostatica
CONTATTATECI PER UNA CONSULENZA GRATUITA
I prodotti e i servizi di KINTEK LAB SOLUTION sono stati riconosciuti da clienti di tutto il mondo. Il nostro personale sarà lieto di assistervi per qualsiasi richiesta. Contattateci per una consulenza gratuita e parlate con uno specialista del prodotto per trovare la soluzione più adatta alle vostre esigenze applicative!