I rivestimenti PVD (Physical Vapor Deposition) sono noti per le loro proprietà sottili, durevoli e ad alte prestazioni. La dimensione o lo spessore dei rivestimenti PVD varia tipicamente tra 0,25 micron e 5 micron, a seconda dell'applicazione e del materiale. Questa sottigliezza garantisce che i rivestimenti non alterino le specifiche delle parti ingegnerizzate fornendo allo stesso tempo eccellente durezza, resistenza alla corrosione e durata. I rivestimenti PVD sono ampiamente utilizzati in settori quali gioielleria, elettronica e produzione grazie alle loro prestazioni superiori rispetto ai metodi di rivestimento tradizionali come la galvanica. Fattori come il materiale del substrato, lo spessore del rivestimento e le condizioni di applicazione influenzano la longevità e l'efficacia dei rivestimenti PVD.
Punti chiave spiegati:
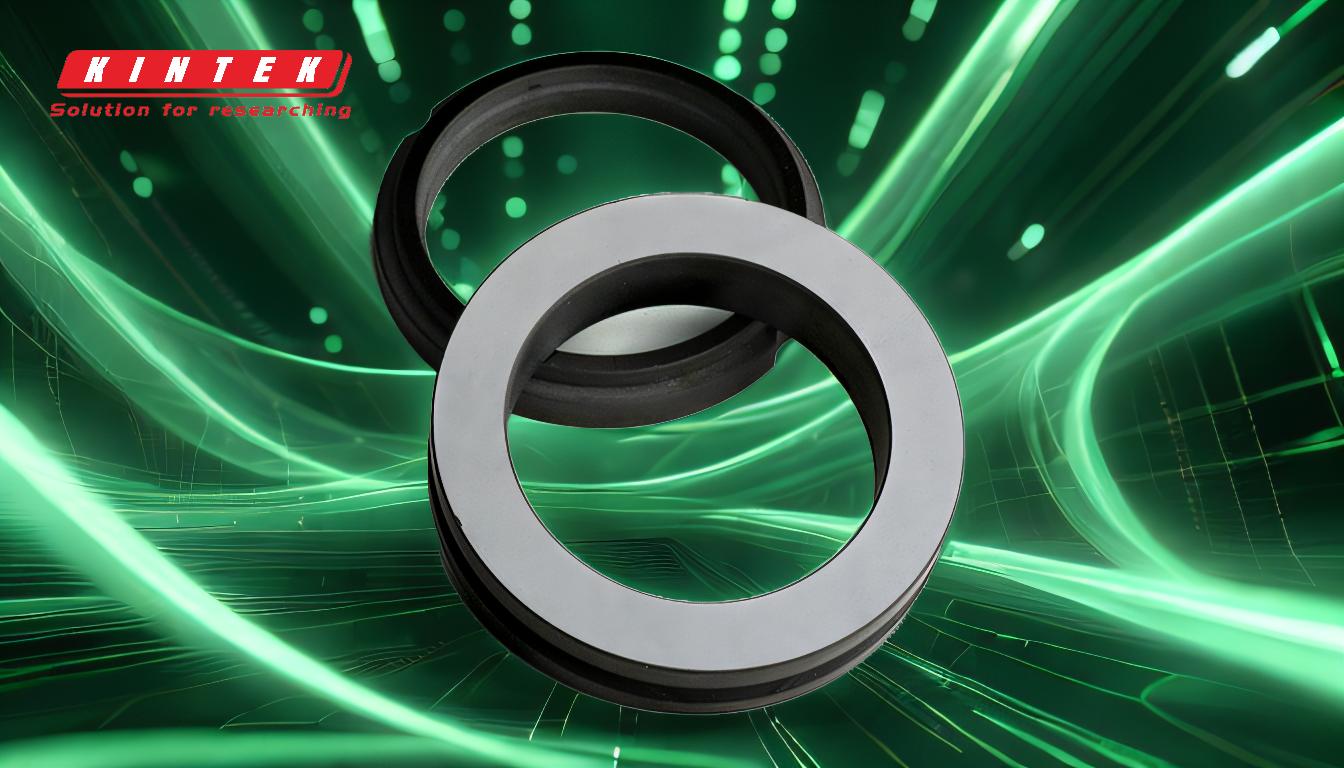
-
Intervallo di spessore tipico dei rivestimenti PVD:
- I rivestimenti PVD sono generalmente molto sottili e vanno da Da 0,25 micron a 5 micron . Questa gamma è significativamente più sottile del diametro di un capello umano, che è di circa 70 micron. Lo spessore sottile garantisce che il rivestimento non alteri le dimensioni o le specifiche del materiale sottostante, rendendolo ideale per applicazioni di precisione.
-
Applicazioni e variazioni di spessore:
-
Lo spessore dei rivestimenti PVD può variare a seconda dell'applicazione. Per esempio:
- In gioielli , lo spessore del rivestimento varia tipicamente da 0,25 micron a 5 micron, fornendo una finitura durevole ed esteticamente gradevole.
- In applicazioni industriali , come il rivestimento dei wafer, gli spessori possono essere fino a 3 nanometri , come si vede nell'esempio di un rivestimento in oro/palladio applicato a un wafer da 6 pollici utilizzando un rivestimento a spruzzo.
-
Lo spessore dei rivestimenti PVD può variare a seconda dell'applicazione. Per esempio:
-
Confronto con altri metodi di rivestimento:
- I rivestimenti PVD sono più sottili di quelli prodotti da Deposizione chimica da fase vapore (CVD) , che tipicamente variano tra 5-10 micron. Nonostante il loro spessore sottile, i rivestimenti PVD sono più duri, più resistenti alla corrosione e più rispettosi dell’ambiente rispetto ai metodi tradizionali come la galvanica e la verniciatura.
-
Durabilità e longevità:
-
I rivestimenti PVD sono noti per la loro durata, che dura ovunque
Da 10 anni a centinaia di anni
a seconda di fattori quali:
- IL materiale del substrato essendo rivestito.
- IL spessore del rivestimento .
- IL condizioni di applicazione , come l'esposizione a temperature elevate o ambienti corrosivi.
-
I rivestimenti PVD sono noti per la loro durata, che dura ovunque
Da 10 anni a centinaia di anni
a seconda di fattori quali:
-
Vantaggi dei rivestimenti PVD:
- Durezza e resistenza alla corrosione: I rivestimenti PVD sono più duri e resistenti alla corrosione rispetto ai rivestimenti galvanici.
- Prestazioni ad alta temperatura: Resistono alle alte temperature e hanno una buona resistenza agli urti.
- Resistenza all'abrasione: Con un ulteriore rivestimento superiore trasparente resistente all'abrasione, i rivestimenti PVD raggiungono un'eccellente resistenza all'usura.
- Rispetto dell'ambiente: Il PVD è un processo più sostenibile ed ecologico rispetto ai metodi di rivestimento tradizionali.
-
Processo di produzione:
-
I rivestimenti PVD sono prodotti da
condensazione dei vapori
di materiali come metalli, carbonio, ceramica, vetro o polimeri su una superficie adatta. Le due tecnologie di rivestimento PVD più utilizzate sono:
- Evaporazione: Prevede il riscaldamento del materiale di rivestimento fino alla sua vaporizzazione e quindi la sua deposizione sul substrato.
- Sputacchiamento: Utilizza un plasma per espellere gli atomi da un materiale bersaglio, che poi si depositano sul substrato.
-
I rivestimenti PVD sono prodotti da
condensazione dei vapori
di materiali come metalli, carbonio, ceramica, vetro o polimeri su una superficie adatta. Le due tecnologie di rivestimento PVD più utilizzate sono:
-
Importanza della magrezza:
- La sottigliezza dei rivestimenti PVD (da 0,5 micron a 5 micron) garantisce che non alterino la specifiche delle parti ingegnerizzate . Ciò è particolarmente importante nei settori in cui la precisione e l'accuratezza dimensionale sono fondamentali, come nel settore elettronico e aerospaziale.
Comprendendo le dimensioni e le proprietà dei rivestimenti PVD, gli acquirenti possono prendere decisioni informate sulla loro idoneità per applicazioni specifiche, garantendo prestazioni e longevità ottimali.
Tabella riassuntiva:
Aspetto chiave | Dettagli |
---|---|
Intervallo di spessore tipico | Da 0,25 micron a 5 micron |
Applicazioni | Gioielleria (0,25-5 micron), Industriale (fino a 3 nanometri) |
Confronto con CVD | Più sottile (5-10 micron per CVD), più duro e più resistente alla corrosione |
Durabilità | Da 10 a centinaia di anni, a seconda del substrato e delle condizioni |
Vantaggi | Elevata durezza, resistenza alla corrosione, prestazioni ad alta temperatura |
Processo di produzione | Evaporazione e sputtering |
Importanza della magrezza | Mantiene le specifiche della parte, ideale per applicazioni di precisione |
Pronto a migliorare le tue applicazioni con i rivestimenti PVD? Contattaci oggi per saperne di più!