Il principio della riduzione dimensionale in un mulino a sfere ruota attorno alle forze meccaniche applicate ai materiali attraverso l'impatto, l'estrusione e l'attrito generati dalle sfere di macinazione all'interno del mulino.Quando il mulino a sfere funziona, le sfere di macinazione si scontrano con il materiale, rompendolo in particelle più piccole.Inoltre, il movimento di rotolamento e di scorrimento delle sfere contro il materiale e le pareti interne del mulino contribuisce a ridurre ulteriormente le dimensioni.Questo processo continua fino al raggiungimento della dimensione desiderata delle particelle.L'efficienza della riduzione dimensionale dipende da fattori quali la velocità del mulino, la dimensione e la quantità delle sfere di macinazione e le proprietà del materiale da lavorare.
Punti chiave spiegati:
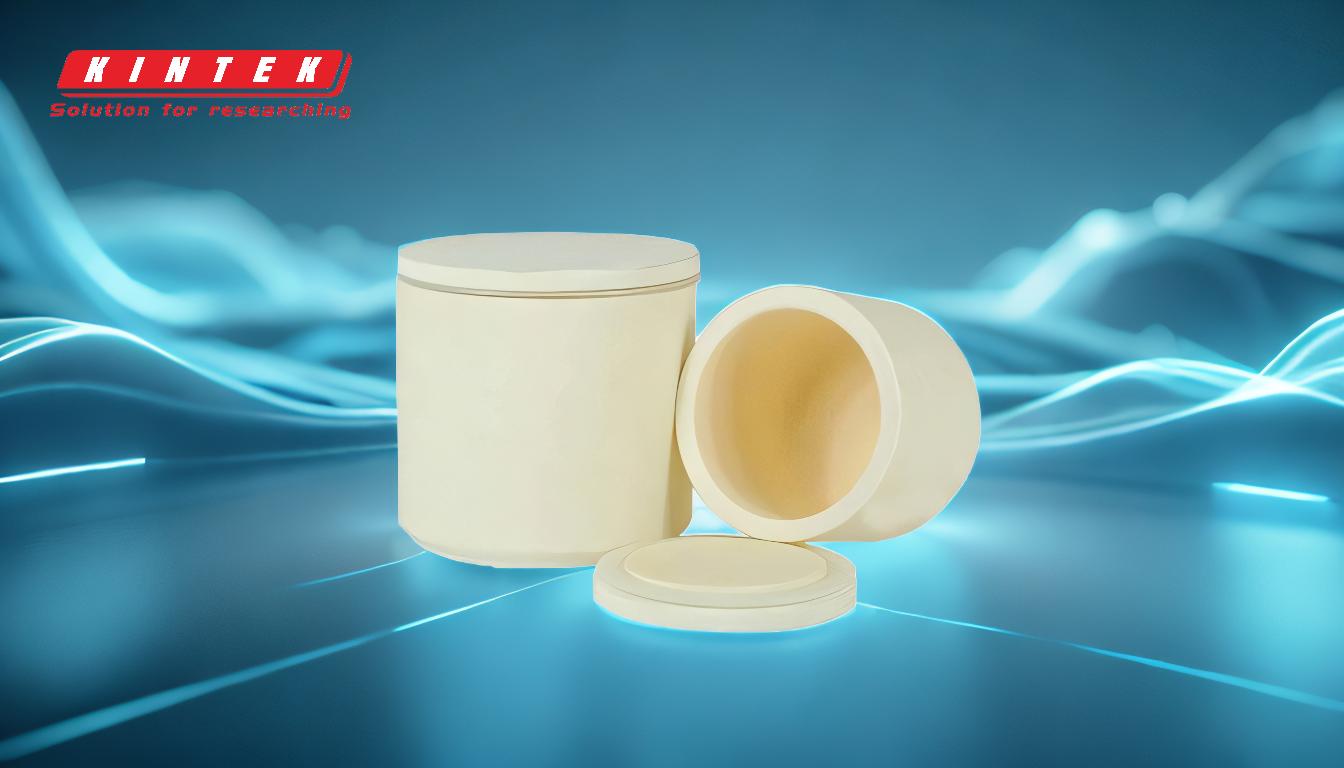
-
Meccanismo di riduzione delle dimensioni:
- Impatto:Le sfere di macinazione entrano in collisione con il materiale, producendo energia cinetica che riduce le particelle in dimensioni più piccole.
- Estrusione:Il materiale viene compresso tra le sfere e le pareti interne del mulino, con conseguente ulteriore riduzione delle dimensioni.
- Attrito:Il movimento di rotolamento e di scorrimento delle sfere contro il materiale genera forze di taglio che aiutano a rompere le particelle.
-
Ruolo delle sfere di macinazione:
- Le sfere di macinazione sono componenti critici che applicano forze meccaniche al materiale.Le loro dimensioni, densità e quantità influenzano l'efficienza del processo di riduzione dimensionale.
- Le sfere più grandi sono più efficaci per la macinazione grossolana, mentre quelle più piccole sono più adatte per la macinazione fine.
-
Parametri operativi:
- Velocità del mulino:La velocità di rotazione del mulino influisce sul movimento delle sfere di macinazione.La velocità ottimale garantisce che le sfere vadano in cascata e colpiscano efficacemente il materiale.
- Rapporto di riempimento:La percentuale del volume del mulino occupata dalle sfere e dal materiale influisce sull'efficienza di macinazione.Un rapporto di riempimento adeguato garantisce un contatto sufficiente tra le sfere e il materiale.
-
Proprietà del materiale:
- La durezza, la fragilità e le dimensioni del materiale da lavorare influenzano il processo di riduzione dimensionale.I materiali più duri possono richiedere tempi di macinazione più lunghi o un maggiore apporto di energia.
-
Controllo del processo:
- La dimensione desiderata delle particelle si ottiene controllando la durata della macinazione e i parametri operativi del mulino.Una volta raggiunta la dimensione desiderata, il processo viene interrotto per evitare una macinazione eccessiva.
-
Applicazioni:
- I mulini a sfere sono ampiamente utilizzati in settori come quello minerario, ceramico e farmaceutico per la macinazione e la miscelazione di materiali al fine di ottenere particelle di dimensioni fini.
Comprendendo questi punti chiave, l'acquirente può prendere decisioni informate sulla scelta del mulino a sfere e dei parametri di macinazione appropriati per la propria applicazione specifica.
Tabella riassuntiva:
Aspetto chiave | Dettagli |
---|---|
Meccanismo di riduzione delle dimensioni | L'impatto, l'estrusione e l'attrito rompono i materiali in particelle più piccole. |
Ruolo delle sfere di macinazione | Le dimensioni, la densità e la quantità influiscono sull'efficienza della macinazione. |
Parametri operativi | La velocità del mulino e il rapporto di riempimento ottimizzano le prestazioni di macinazione. |
Proprietà del materiale | La durezza e la fragilità influenzano il tempo di macinazione e i requisiti energetici. |
Controllo del processo | Controllo della durata e dei parametri di macinazione per ottenere le dimensioni desiderate delle particelle. |
Applicazioni | Utilizzato nei settori minerario, ceramico e farmaceutico per la produzione di particelle fini. |
Scoprite come un mulino a sfere può ottimizzare la lavorazione dei vostri materiali... contattate i nostri esperti oggi stesso !