Il processo di sputtering, pur essendo ampiamente utilizzato per la deposizione di film sottili, presenta diversi svantaggi degni di nota.Tra questi, i bassi tassi di deposizione, gli alti costi operativi e di capitale, i rischi di contaminazione del film e le difficoltà di compatibilità dei materiali.Inoltre, lo sputtering può portare a un uso inefficiente del materiale, a uno spessore non uniforme del film e a difficoltà di integrazione con alcuni processi di fabbricazione come il lift-off.Il processo genera anche un notevole calore, che richiede sistemi di raffreddamento robusti, ed è meno efficace per i materiali isolanti.Questi inconvenienti rendono lo sputtering meno adatto a specifiche applicazioni, in particolare a quelle che richiedono alta precisione, economicità o compatibilità con materiali sensibili.
Punti chiave spiegati:
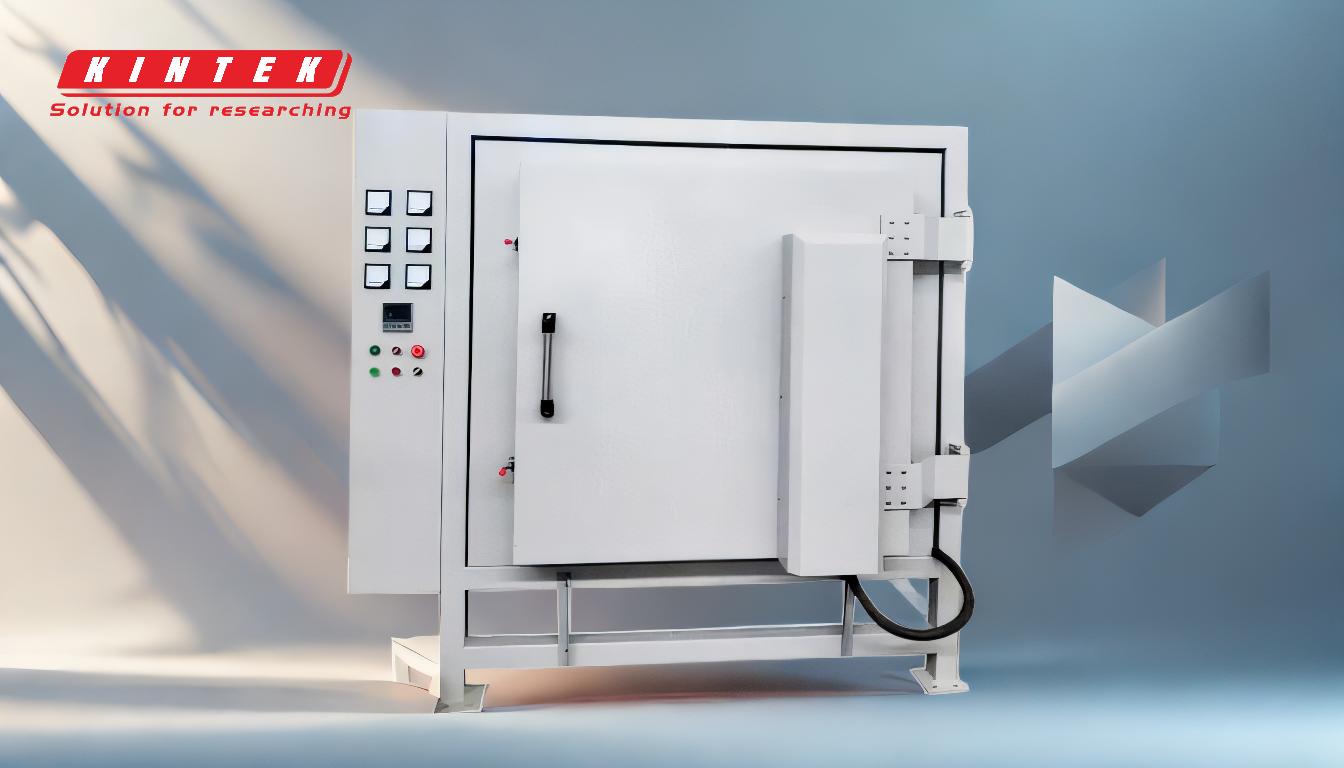
-
Bassi tassi di deposizione
- Lo sputtering ha generalmente tassi di deposizione più bassi rispetto ad altri metodi come l'evaporazione termica.
- Questa limitazione è particolarmente pronunciata per materiali come il SiO2, dove il raggiungimento degli spessori desiderati può richiedere molto tempo.
- I tassi di deposizione lenti possono aumentare i tempi e i costi di produzione, rendendo lo sputtering meno efficiente per le applicazioni ad alta produttività.
-
Alti costi di capitale e operativi
- Le apparecchiature per lo sputtering sono costose e richiedono un investimento iniziale significativo.
- Anche i costi di manutenzione sono elevati a causa della necessità di sistemi di vuoto specializzati e di meccanismi di raffreddamento per gestire il calore generato durante il processo.
- I target utilizzati nello sputtering sono spesso costosi e l'utilizzo dei materiali può essere inefficiente, aumentando ulteriormente le spese.
-
Rischi di contaminazione del film
- Lo sputtering opera in un intervallo di vuoto inferiore rispetto all'evaporazione, aumentando la probabilità che le impurità entrino nel substrato.
- I contaminanti gassosi presenti nel plasma possono attivarsi, causando la contaminazione del film depositato.
- Lo sputtering reattivo richiede un controllo preciso della composizione del gas per evitare l'avvelenamento del bersaglio, aggiungendo complessità e rischi.
-
Spessore del film non uniforme
- La distribuzione del flusso di deposizione nello sputtering è spesso non uniforme e richiede l'uso di attrezzature mobili per ottenere uno spessore costante del film.
- Ciò aggiunge complessità al processo e può portare a incongruenze nella qualità del film se non viene gestito con attenzione.
-
Generazione di calore e riscaldamento del substrato
- La maggior parte dell'energia incidente sul bersaglio viene convertita in calore, che deve essere efficacemente rimosso per evitare danni al substrato o alle apparecchiature.
- L'elevato riscaldamento del substrato può limitare i tipi di materiali che possono essere rivestiti, in particolare quelli sensibili alla temperatura.
-
Problemi di compatibilità dei materiali
- Lo sputtering non è adatto ai materiali isolanti, in quanto possono accumulare carica e interrompere il processo.
- I solidi organici e altri materiali sensibili possono degradarsi sotto il bombardamento ionico, limitando la gamma di materiali che possono essere efficacemente sottoposti a sputtering.
-
Sfide nell'integrazione con i processi Lift-Off
- Il trasporto diffuso degli atomi sputati rende difficile ottenere un'ombreggiatura completa, complicando l'integrazione dello sputtering con i processi lift-off per la strutturazione dei film.
- Questo può portare a problemi di contaminazione e ridurre la precisione del prodotto finale.
-
Difficoltà nel controllo attivo della crescita strato per strato
- Rispetto a metodi come la deposizione laser pulsata, lo sputtering offre un minore controllo sulla crescita strato per strato.
- Questa limitazione può influire sulla qualità e sull'uniformità dei film multistrato, in particolare nelle applicazioni che richiedono un controllo preciso a livello atomico.
-
Impurità del gas inerte
- I gas inerti di sputtering, come l'argon, possono rimanere intrappolati nel film in crescita sotto forma di impurità.
- Queste impurità possono influire sulle proprietà meccaniche, elettriche o ottiche del film depositato, compromettendone potenzialmente le prestazioni.
-
Limitazioni dei parametri di processo
- Lo sputtering è condizionato dalla realtà dei sistemi a vuoto, che limitano la gamma di parametri di processo utilizzabili.
- Ciò può limitare la versatilità del processo e renderlo meno adattabile a requisiti applicativi specifici.
In sintesi, sebbene lo sputtering sia una tecnica versatile e ampiamente utilizzata per la deposizione di film sottili, i suoi svantaggi - come i bassi tassi di deposizione, i costi elevati, i rischi di contaminazione e i problemi di compatibilità dei materiali - possono limitarne l'idoneità per alcune applicazioni.Un'attenta considerazione di questi inconvenienti è essenziale quando si sceglie un metodo di deposizione per specifiche esigenze industriali o di ricerca.
Tabella riassuntiva:
Svantaggio | Dettagli chiave |
---|---|
Bassa velocità di deposizione | Più lento dell'evaporazione termica; aumenta i tempi e i costi di produzione. |
Costi operativi e di capitale elevati | Apparecchiature costose, manutenzione elevata e utilizzo inefficiente dei materiali. |
Rischi di contaminazione del film | Un intervallo di vuoto più basso aumenta i rischi di impurità; lo sputtering reattivo aggiunge complessità. |
Spessore del film non uniforme | Richiede l'uso di attrezzature mobili; può portare a una qualità del film incoerente. |
Generazione di calore | Il calore elevato richiede sistemi di raffreddamento robusti; limita i materiali sensibili alla temperatura. |
Problemi di compatibilità dei materiali | Non adatto agli isolanti e ai materiali sensibili; rischi di degradazione. |
Sfide per l'integrazione | Difficoltà nei processi di sollevamento; problemi di contaminazione e precisione. |
Controllo limitato strato per strato | Minore controllo rispetto alla deposizione laser pulsata; influisce sull'uniformità del multistrato. |
Impurità del gas inerte | Le impurità dell'argon possono compromettere le proprietà del film. |
Limitazioni dei parametri di processo | I vincoli del sistema del vuoto limitano la versatilità e l'adattabilità. |
Avete bisogno di una soluzione migliore per la deposizione di film sottili? Contattateci oggi stesso per esplorare le alternative!