La velocità di un mulino a sfere è un fattore critico che influenza le prestazioni di macinazione e l'efficienza complessiva. A basse velocità, le sfere di macinazione tendono a scivolare o a rotolare l'una sull'altra, riducendo al minimo le dimensioni. Al contrario, a velocità elevate, la forza centrifuga fa sì che le sfere vengano scagliate contro la parete del cilindro, impedendo una macinazione efficace. Le prestazioni ottimali si ottengono a velocità normali, dove le sfere vengono portate in cima al mulino e poi scendono a cascata, massimizzando la riduzione delle dimensioni. Inoltre, altri fattori come il diametro del tamburo, il rapporto tra diametro e lunghezza del tamburo e le proprietà del materiale da macinare giocano un ruolo importante nel determinare la produttività di un mulino a sfere.
Punti chiave spiegati:
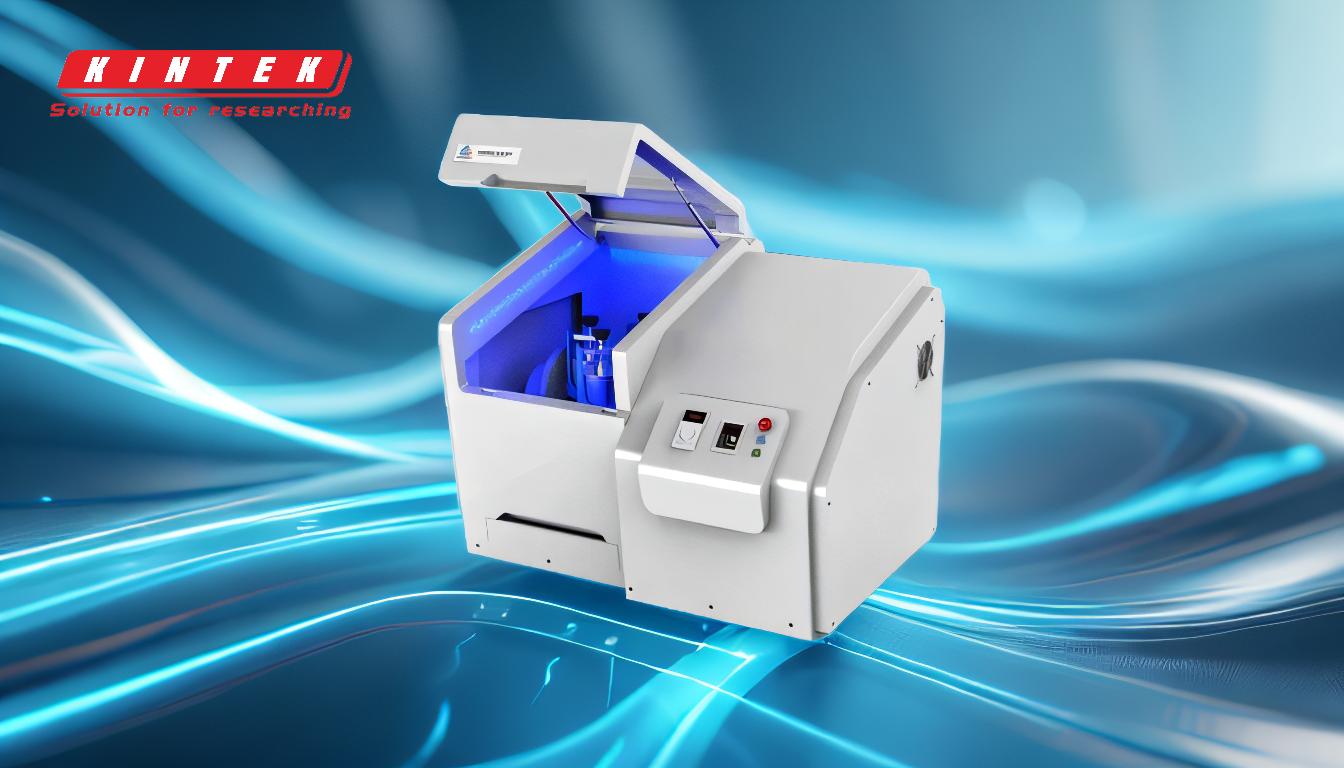
-
Impatto della velocità sull'efficienza di macinazione:
- Bassa velocità: A basse velocità di rotazione, le sfere di macinazione tendono a scivolare o rotolare l'una sull'altra. Ciò comporta forze di impatto e di taglio minime, con conseguente inefficienza della macinazione e riduzione minima delle dimensioni.
- Alta velocità: Quando il mulino funziona ad alta velocità, la forza centrifuga diventa dominante. Le sfere vengono scagliate contro la parete del cilindro e non scendono a cascata, il che impedisce una macinazione efficace poiché non si verifica un impatto o un'abrasione significativi.
- Velocità normale: A velocità ottimale, le sfere vengono sollevate a una certa altezza prima di scendere a cascata. Questo effetto a cascata crea una combinazione di forze di impatto e abrasione, che porta alla massima riduzione delle dimensioni e a una macinazione efficiente.
-
Velocità ottimale per la massima efficienza:
- La velocità ottimale per un mulino a sfere è in genere definita "velocità critica", in cui le sfere vengono portate in cima al mulino e poi scendono a cascata. Questa velocità critica si aggira solitamente intorno al 65-75% della velocità critica del mulino, a seconda del progetto del mulino e del materiale da macinare.
- Il funzionamento a questa velocità assicura che i mezzi di macinazione (sfere) siano in costante movimento, creando le forze di impatto e di taglio necessarie per frantumare efficacemente il materiale.
-
Altri fattori che influenzano le prestazioni del mulino a sfere:
- Diametro e lunghezza del tamburo: Il rapporto tra il diametro del tamburo e la sua lunghezza (rapporto L:D) è fondamentale. Un rapporto L:D ottimale di 1,56-1,64 è generalmente consigliato per una macinazione efficiente.
- Mezzo di macinazione: Le dimensioni e il tipo di sfere di macinazione utilizzate nel mulino possono influire in modo significativo sull'efficienza della macinazione. Le sfere più grandi sono più efficaci per la macinazione grossolana, mentre quelle più piccole sono migliori per la macinazione fine.
- Proprietà del materiale: Anche le proprietà fisiche e chimiche del materiale da macinare, come la durezza, il contenuto di umidità e la distribuzione delle dimensioni delle particelle, influiscono sulle prestazioni di macinazione.
- Rapporto di riempimento: La percentuale del volume del mulino riempito con il mezzo di macinazione (sfere) influisce sull'efficienza di macinazione. Un rapporto di riempimento ottimale garantisce un contatto sufficiente tra le sfere e il materiale da macinare senza sovraccaricare il mulino.
- Forma della superficie della corazza: La forma e le condizioni della superficie interna del mulino (armatura) possono influenzare il movimento delle sfere e l'efficienza del processo di macinazione.
- Rimozione tempestiva del prodotto macinato: La rimozione efficiente del prodotto macinato dal mulino è essenziale per evitare una macinazione eccessiva e per mantenere condizioni di macinazione ottimali.
-
Implicazioni pratiche per gli acquirenti di apparecchiature:
- Controllo della velocità: Quando si sceglie un mulino a sfere, è fondamentale assicurarsi che il mulino abbia un controllo della velocità regolabile per operare alla velocità ottimale per i diversi materiali e requisiti di macinazione.
- Design del mulino: Considerare il rapporto tra diametro e lunghezza del tamburo, nonché il design della superficie di armatura, per garantire una macinazione efficiente.
- Mezzo di macinazione: Scegliere le dimensioni e il tipo di sfere di macinazione appropriate in base al materiale da macinare e alla finezza desiderata del prodotto.
- Rapporto di riempimento: Assicurarsi che il mulino possa funzionare con un rapporto di riempimento ottimale per massimizzare l'efficienza di macinazione.
- Gestione del materiale: Considerare la facilità di caricamento del materiale e di rimozione del prodotto per mantenere un funzionamento continuo ed efficiente.
In sintesi, la velocità di un mulino a sfere è un parametro fondamentale che influisce direttamente sulle sue prestazioni di macinazione. Il funzionamento alla velocità ottimale garantisce un'efficiente riduzione delle dimensioni, mentre altri fattori come il design del mulino, il mezzo di macinazione e le proprietà del materiale giocano un ruolo significativo nel determinare la produttività complessiva del mulino. Gli acquirenti di apparecchiature devono considerare attentamente questi fattori per scegliere un mulino a sfere che soddisfi le loro specifiche esigenze di macinazione.
Tabella riassuntiva:
Fattore | Impatto sull'efficienza di macinazione |
---|---|
Bassa velocità | Impatto e forze di taglio minime, con conseguente inefficienza della macinazione e riduzione minima delle dimensioni. |
Alta velocità | La forza centrifuga scaraventa le sfere contro la parete, impedendo una macinazione efficace. |
Velocità normale | Le sfere scendono a cascata, creando forze di impatto e abrasione per la massima riduzione delle dimensioni. |
Velocità critica | In genere il 65-75% della velocità critica del mulino, per garantire prestazioni di macinazione ottimali. |
Diametro/Lunghezza del tamburo | Il rapporto L:D ottimale (1,56-1,64) aumenta l'efficienza di macinazione. |
Mezzo di macinazione | Sfere più grandi per la macinazione grossolana; sfere più piccole per la macinazione fine. |
Proprietà del materiale | Durezza, umidità e distribuzione granulometrica influiscono sulle prestazioni di macinazione. |
Rapporto di riempimento | Il riempimento ottimale garantisce un contatto sufficiente tra le sfere e il materiale senza sovraccaricarlo. |
Forma della superficie della corazza | Influenza il movimento delle sfere e l'efficienza di macinazione. |
Rimozione del prodotto | La rimozione tempestiva impedisce una macinazione eccessiva e mantiene le condizioni ottimali. |
Siete pronti a ottimizzare il vostro processo di macinazione? Contattateci oggi stesso per trovare il mulino a sfere perfetto per le vostre esigenze!