I rivestimenti PVD (Physical Vapor Deposition) e DLC (Diamond-Like Carbon) sono entrambi tecnologie avanzate per il trattamento delle superfici, ma differiscono in modo significativo per composizione, applicazione e caratteristiche prestazionali.PVD è un termine generale per indicare una serie di processi di rivestimento che depositano film sottili di materiali, tra cui metalli, leghe e ceramiche, su un substrato in un ambiente sotto vuoto.Il DLC, invece, è un tipo specifico di rivestimento che consiste in una forma di carbonio amorfo con proprietà simili al diamante, come l'elevata durezza e il basso attrito.Mentre il PVD può essere utilizzato per applicare un'ampia gamma di materiali, i rivestimenti DLC sono specificamente progettati per fornire un'eccezionale resistenza all'usura, un basso attrito e un'elevata durezza, rendendoli ideali per le applicazioni che richiedono durata e prestazioni estreme.
Punti chiave spiegati:
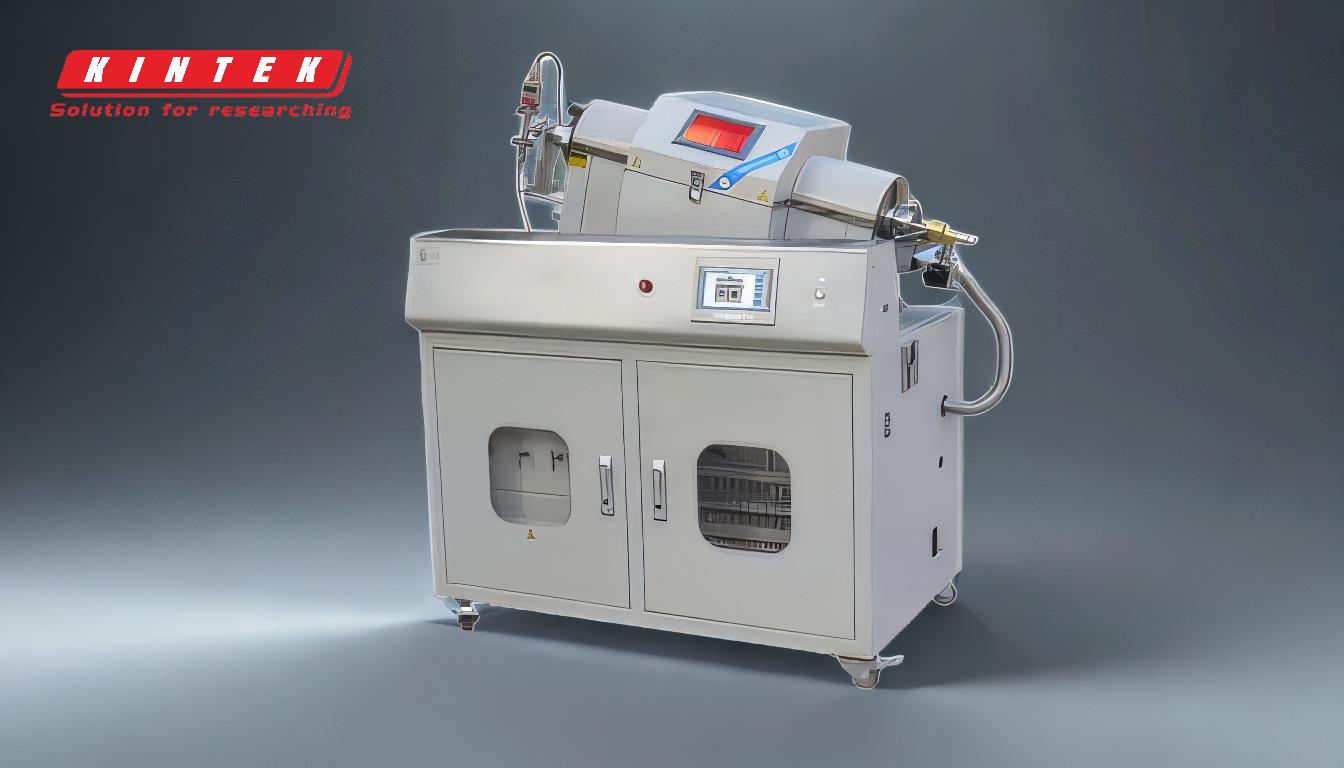
-
Composizione e differenze di materiale:
- Rivestimento PVD:Il PVD può depositare un'ampia gamma di materiali, tra cui metalli, leghe e ceramiche.Il processo prevede la vaporizzazione fisica del materiale di rivestimento, che viene poi depositato sul substrato in un ambiente sotto vuoto.
- Rivestimento DLC:Il DLC è un tipo specifico di rivestimento a base di carbonio amorfo, con proprietà simili al diamante.È caratterizzato da elevata durezza, basso attrito ed eccellente resistenza all'usura.I rivestimenti DLC sono generalmente applicati con tecniche PVD o CVD (Chemical Vapor Deposition).
-
Processi di applicazione:
- Rivestimento PVD:I processi PVD avvengono in una camera a vuoto ad alte temperature.Il materiale di rivestimento viene vaporizzato con metodi fisici, come lo sputtering o l'evaporazione, e poi depositato sul substrato.Questo processo consente l'applicazione di un'ampia varietà di materiali.
- Rivestimento DLC:I rivestimenti DLC vengono solitamente applicati con tecniche PVD o CVD.Nella PVD, la fonte di carbonio viene vaporizzata e depositata sul substrato, mentre nella CVD viene utilizzata una reazione chimica per depositare il film di carbonio.Entrambi i metodi consentono di ottenere un rivestimento duro e resistente con proprietà simili al diamante.
-
Caratteristiche delle prestazioni:
- Rivestimento PVD:I rivestimenti PVD sono noti per la loro elevata purezza, uniformità ed eccellente adesione al substrato.Spesso sono più duri e resistenti alla corrosione rispetto ai rivestimenti applicati per elettrodeposizione.I rivestimenti PVD offrono inoltre un'elevata resistenza alle temperature e agli urti, un'eccellente resistenza all'abrasione e una lunga durata.
- Rivestimento DLC:I rivestimenti DLC sono progettati specificamente per offrire un'eccezionale resistenza all'usura, un basso attrito e un'elevata durezza.Queste proprietà rendono i rivestimenti DLC ideali per le applicazioni che richiedono durata e prestazioni estreme, come nel settore automobilistico e aerospaziale.
-
Impatto ambientale:
- Rivestimento PVD:Il PVD è considerato un'alternativa più ecologica ai processi di rivestimento tradizionali come la cromatura.Produce rivestimenti durevoli e di lunga durata senza generare sostanze tossiche, il che lo rende una scelta etica per proteggere le parti di veicoli e altri prodotti.
- Rivestimento DLC:I rivestimenti DLC sono anche ecologici, in quanto non producono sottoprodotti nocivi durante il processo di rivestimento.L'uso di rivestimenti DLC può ridurre la necessità di lubrificanti e altri tipi di manutenzione, contribuendo ulteriormente alla sostenibilità ambientale.
-
Applicazioni:
- Rivestimento PVD:I rivestimenti PVD sono utilizzati in un'ampia gamma di applicazioni, tra cui i rivestimenti a film sottile per il fotovoltaico, i dispositivi a semiconduttore, i dispositivi di visione, la ricerca e i dispositivi medici, la ricerca sulla corrosione, i rivestimenti antiriflesso, gli studi sulle interazioni interfacciali, le applicazioni aerospaziali e automobilistiche ad alte prestazioni e la deposizione di film su vari substrati, compresi i polimeri.
- Rivestimento DLC:I rivestimenti DLC sono particolarmente utili nelle applicazioni che richiedono estrema durata e prestazioni, come ad esempio nei componenti automobilistici (ad esempio, parti del motore, componenti della trasmissione), negli utensili da taglio e nei dispositivi medici.Il basso attrito e l'elevata durezza dei rivestimenti DLC li rendono ideali per ridurre l'usura e prolungare la durata dei componenti critici.
In sintesi, i rivestimenti PVD e DLC offrono soluzioni avanzate per il trattamento delle superfici, ma si differenziano per la composizione, i processi di applicazione e le caratteristiche prestazionali.I rivestimenti PVD sono versatili e possono essere utilizzati per applicare un'ampia gamma di materiali, mentre i rivestimenti DLC sono progettati specificamente per fornire un'eccezionale resistenza all'usura, un basso attrito e un'elevata durezza, rendendoli ideali per le applicazioni più impegnative.Entrambi i tipi di rivestimento sono rispettosi dell'ambiente e offrono vantaggi significativi rispetto ai metodi di rivestimento tradizionali.
Tabella riassuntiva:
Aspetto | Rivestimento PVD | Rivestimento DLC |
---|---|---|
Composizione | Metalli, leghe, ceramiche | Carbonio amorfo con proprietà diamantate |
Processo di applicazione | Vaporizzazione in camera a vuoto (sputtering/evaporazione) | Tecniche PVD o CVD per la deposizione di carbonio |
Prestazioni | Elevata purezza, uniformità, resistenza alla corrosione, durevolezza | Eccezionale resistenza all'usura, basso attrito, elevata durezza |
Impatto ambientale | Ecologico, senza sottoprodotti tossici | Ecologico, riduce la necessità di lubrificanti |
Applicazioni | Fotovoltaico, semiconduttori, dispositivi medici, aerospaziale, automotive | Componenti automobilistici, utensili da taglio, dispositivi medici |
Avete bisogno di aiuto per scegliere il rivestimento giusto per la vostra applicazione? Contattate i nostri esperti oggi stesso per una consulenza personalizzata!