Lo stampaggio a iniezione è un processo produttivo utilizzato per produrre pezzi iniettando materiale fuso in uno stampo.Il processo è altamente efficiente e può essere suddiviso in quattro fasi principali: bloccaggio, iniezione, raffreddamento ed espulsione.Ogni fase svolge un ruolo critico nel garantire che il prodotto finale soddisfi le specifiche desiderate.L'intero ciclo dura in genere da 2 secondi a 2 minuti, a seconda della complessità del pezzo e del materiale utilizzato.Di seguito analizzeremo in dettaglio ogni fase per fornire una comprensione completa del processo di stampaggio a iniezione.
Punti chiave spiegati:
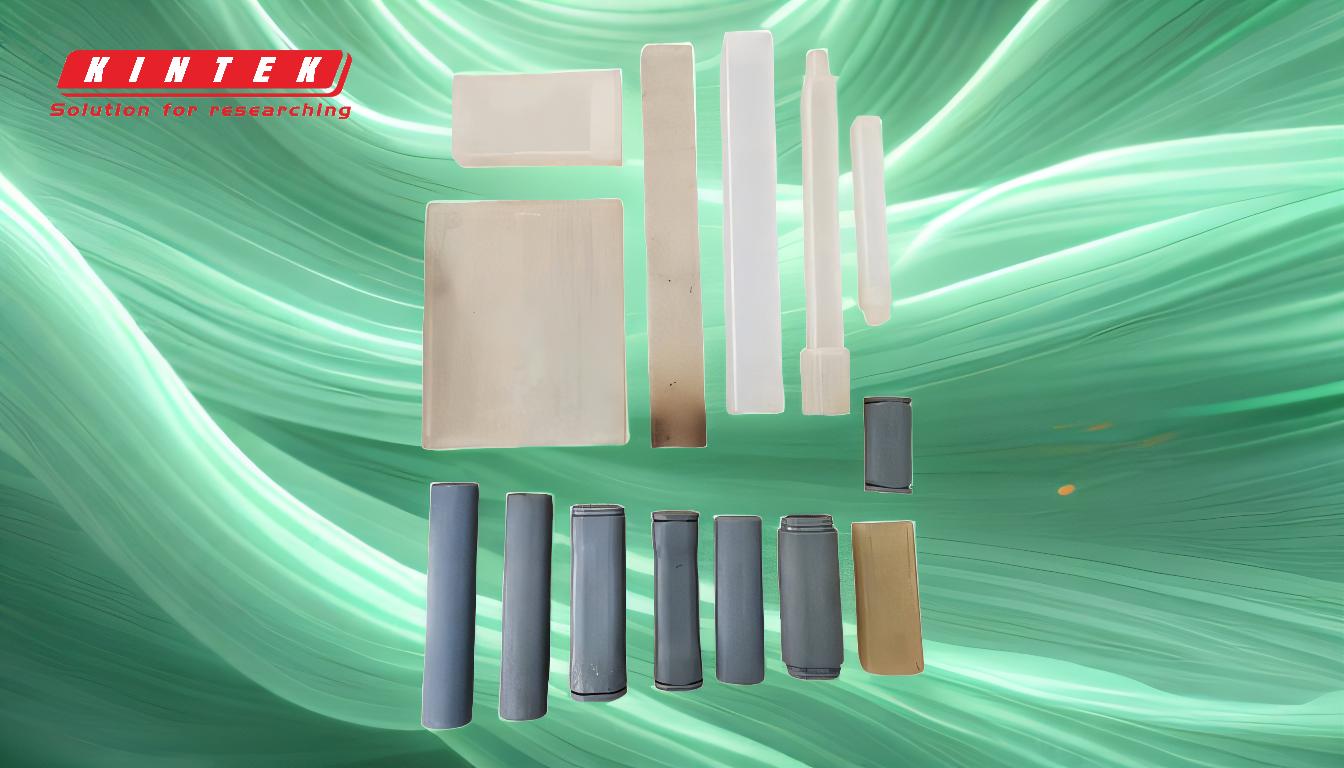
-
Fase di serraggio
- Scopo:La fase di bloccaggio consiste nel fissare insieme le due metà dello stampo per preparare l'iniezione del materiale fuso.
-
Processo:
- Lo stampo è composto da due metà: la metà stazionaria (fissata alla pressa a iniezione) e la metà mobile (che si apre e si chiude).
- Un'unità di bloccaggio applica una pressione per tenere le metà dello stampo saldamente unite durante il processo di iniezione.
- La forza di serraggio deve essere sufficiente a sopportare la pressione del materiale iniettato, evitando perdite o deformazioni dello stampo.
- Importanza:Un corretto bloccaggio assicura che lo stampo rimanga chiuso e stabile, il che è fondamentale per produrre pezzi di alta qualità con dimensioni precise.
-
Fase di iniezione
- Scopo:In questa fase, il materiale fuso viene iniettato nella cavità dello stampo per formare il pezzo desiderato.
-
Processo:
- Il materiale (di solito pellet di plastica) viene introdotto in un cilindro riscaldato, dove viene fuso e omogeneizzato.
- Una vite o uno stantuffo alternativo spinge il materiale fuso nella cavità dello stampo ad alta pressione.
- Il materiale riempie la cavità, assumendo la forma dello stampo.
-
Fattori da considerare:
- La pressione di iniezione, la velocità e la temperatura devono essere attentamente controllate per garantire che il materiale riempia lo stampo in modo completo e uniforme.
- Un riempimento eccessivo o insufficiente dello stampo può causare difetti come deformazioni, segni di affossamento o parti incomplete.
- Importanza:La fase di iniezione determina la forma e l'integrità iniziali del pezzo, rendendola una fase critica del processo.
-
Fase di raffreddamento
- Scopo:Dopo il riempimento dello stampo, il materiale deve raffreddarsi e solidificarsi per mantenere la forma.
-
Processo:
- Il raffreddamento inizia non appena il materiale viene iniettato nello stampo.
- Lo stampo è progettato con canali di raffreddamento attraverso i quali circola un refrigerante (solitamente acqua) per dissipare il calore.
- Il tempo di raffreddamento dipende dalle proprietà del materiale, dallo spessore del pezzo e dal design dello stampo.
-
Fattori da considerare:
- Un raffreddamento insufficiente può provocare deformazioni o tensioni interne al pezzo.
- Un raffreddamento eccessivo può aumentare il tempo di ciclo, riducendo l'efficienza produttiva.
- Importanza:Un raffreddamento adeguato garantisce la corretta solidificazione del pezzo, mantenendo l'accuratezza dimensionale e l'integrità strutturale.
-
Fase di espulsione
- Scopo:Una volta che il pezzo si è raffreddato e solidificato, viene espulso dallo stampo.
-
Processo:
- Lo stampo si apre e i perni o le piastre di espulsione spingono il pezzo fuori dalla cavità dello stampo.
- Il pezzo viene quindi rimosso dalla macchina, manualmente o automaticamente.
-
Fattori da considerare:
- L'espulsione deve essere eseguita con attenzione per evitare di danneggiare il pezzo o lo stampo.
- Un'adeguata progettazione dello stampo, compreso il posizionamento dei perni di espulsione, è fondamentale per garantire un'espulsione senza problemi.
- Importanza:La fase di espulsione completa il ciclo, consentendo di preparare lo stampo per l'iniezione successiva.
Ulteriori considerazioni per gli acquirenti di attrezzature e materiali di consumo:
- Selezione del materiale:Il tipo di materiale utilizzato (ad esempio, termoplastici, polimeri termoindurenti) influisce sul processo di stampaggio e sulle proprietà del prodotto finale.
- Progettazione dello stampo:Uno stampo ben progettato con canali di raffreddamento e meccanismi di espulsione adeguati è essenziale per una produzione efficiente.
- Specifiche della macchina:La macchina per lo stampaggio a iniezione deve avere una forza di chiusura, una pressione di iniezione e una capacità di raffreddamento adeguate per gestire i requisiti specifici del pezzo.
- Ottimizzazione del tempo di ciclo:Ridurre il tempo di ciclo mantenendo la qualità è fondamentale per migliorare l'efficienza produttiva e ridurre i costi.
Comprendendo queste fasi e la loro importanza, gli acquirenti di attrezzature e materiali di consumo possono prendere decisioni informate per ottimizzare il processo di stampaggio a iniezione per le loro esigenze specifiche.
Tabella riassuntiva:
Fase | Scopo | Processo chiave | Importanza |
---|---|---|---|
Serraggio | Fissare le metà dello stampo per l'iniezione | Applicare una forza di serraggio per tenere lo stampo ben saldo; evitare perdite o deformazioni | Assicura la stabilità dello stampo e la precisione delle dimensioni dei pezzi |
Iniezione | Iniettare il materiale fuso nella cavità dello stampo | Fondere il materiale, spingerlo nello stampo ad alta pressione; controllare pressione, velocità e temperatura. | Determina la forma e l'integrità del pezzo; è fondamentale per ottenere risultati privi di difetti. |
Raffreddamento | Solidificare il materiale per mantenere la forma | Far circolare il refrigerante attraverso i canali dello stampo; controllare il tempo di raffreddamento in base al materiale e allo spessore del pezzo | Assicura l'accuratezza dimensionale e l'integrità strutturale; previene la deformazione |
Espulsione | Rimuovere la parte solidificata dallo stampo | Aprire lo stampo e utilizzare i perni/piastre di espulsione per spingere fuori la parte; assicurare un'espulsione uniforme | Completa il ciclo; prepara lo stampo per l'iniezione successiva |
Siete pronti a ottimizzare il vostro processo di stampaggio a iniezione? Contattate oggi stesso i nostri esperti per soluzioni su misura!