Il processo di stampaggio a iniezione è una tecnica di produzione utilizzata per produrre pezzi iniettando materiale fuso in uno stampo.Il processo dura in genere da 2 secondi a 2 minuti e consiste in quattro fasi principali: bloccaggio, iniezione, raffreddamento ed espulsione.Ciascuna fase svolge un ruolo critico nel garantire che il prodotto finale soddisfi le specifiche desiderate.La comprensione di queste fasi è essenziale per ottimizzare il processo di stampaggio, ridurre i difetti e migliorare l'efficienza.
Punti chiave spiegati:
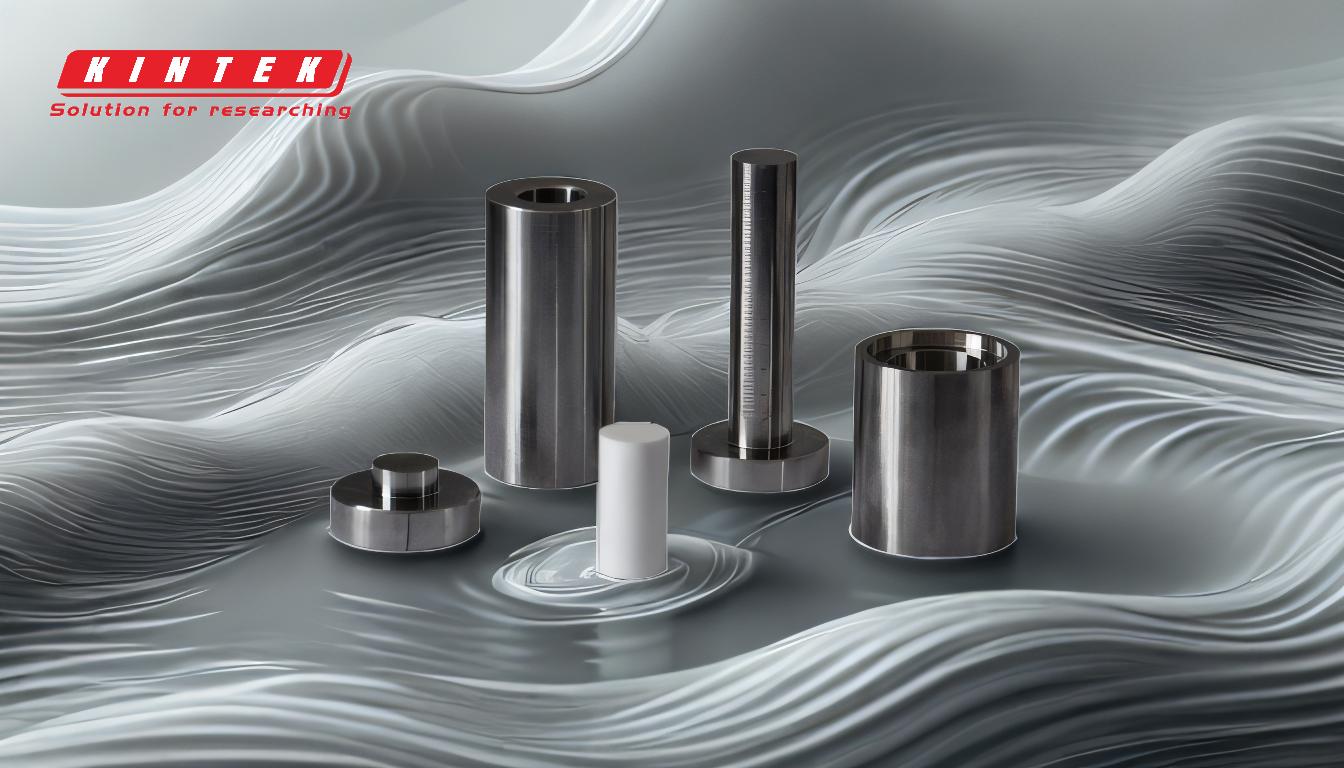
-
Fase di serraggio:
- Scopo:La fase di chiusura è il primo passo del processo di stampaggio a iniezione.Il suo scopo principale è quello di chiudere saldamente le due metà dello stampo per preparare l'iniezione del materiale fuso.
- Processo:Lo stampo viene montato sulla pressa a iniezione e l'unità di bloccaggio tiene insieme le metà dello stampo con una forza sufficiente a resistere alla pressione del materiale iniettato.La forza di serraggio necessaria dipende dalle dimensioni e dalla complessità del pezzo da produrre.
- Importanza:Un corretto serraggio assicura che lo stampo rimanga chiuso durante le fasi di iniezione e raffreddamento, evitando difetti come il flash (materiale in eccesso che fuoriesce dalla cavità dello stampo).
-
Fase di iniezione:
- Scopo:La fase di iniezione prevede l'introduzione di materiale fuso nella cavità dello stampo.Questa fase è fondamentale per dare forma al prodotto finale.
- Il processo:Il materiale, in genere sotto forma di pellet, viene introdotto nel cilindro della pressa a iniezione, dove viene riscaldato fino a raggiungere lo stato fuso.Il materiale fuso viene quindi iniettato nella cavità dello stampo ad alta pressione.La velocità di iniezione, la pressione e la temperatura sono attentamente controllate per garantire che il materiale riempia lo stampo in modo completo e uniforme.
- Importanza:La fase di iniezione determina la qualità della finitura superficiale, la precisione dimensionale e l'integrità strutturale del pezzo.Un'iniezione inadeguata può portare a difetti come la mancanza di colpi (riempimento incompleto dello stampo) o i segni di affossamento (depressioni sulla superficie).
-
Fase di raffreddamento:
- Scopo:La fase di raffreddamento consente al materiale fuso di solidificarsi all'interno dello stampo, assumendo la forma della cavità dello stampo.
- Processo:Dopo il riempimento della cavità dello stampo, il materiale inizia a raffreddarsi e a solidificarsi.Il tempo di raffreddamento varia a seconda del materiale utilizzato, dello spessore del pezzo e del design dello stampo.Il raffreddamento è in genere facilitato da canali di raffreddamento all'interno dello stampo che fanno circolare acqua o altri mezzi di raffreddamento.
- Importanza:Un raffreddamento adeguato è essenziale per garantire che il pezzo mantenga la sua forma e stabilità dimensionale.Un raffreddamento insufficiente può provocare deformazioni, ritiri o tensioni interne al pezzo.
-
Fase di espulsione:
- Scopo:La fase di espulsione consiste nel rimuovere il pezzo solidificato dallo stampo.
- Processo:Una volta che il materiale si è raffreddato e solidificato a sufficienza, lo stampo si apre e i perni o le piastre di espulsione spingono il pezzo fuori dalla cavità dello stampo.Il pezzo viene quindi raccolto e lo stampo si richiude per prepararsi al ciclo successivo.
- Importanza:La fase di espulsione deve essere gestita con attenzione per evitare di danneggiare il pezzo o lo stampo.Un'espulsione corretta garantisce che il pezzo venga rilasciato senza problemi e senza difetti come graffi o deformazioni.
Sintesi:
Il processo di stampaggio a iniezione è un metodo altamente efficiente per produrre pezzi con geometrie complesse e alta precisione.Le quattro fasi - bloccaggio, iniezione, raffreddamento ed espulsione - sono parte integrante del successo del processo.Ogni fase deve essere attentamente controllata per garantire la produzione di pezzi di alta qualità.La comprensione di queste fasi consente ai produttori di ottimizzare il processo di stampaggio, ridurre i difetti e migliorare l'efficienza complessiva.
Tabella riassuntiva:
Fase | Scopo | Dettagli chiave |
---|---|---|
Serraggio | Chiude in modo sicuro lo stampo per prepararlo all'iniezione. | Assicura che lo stampo rimanga chiuso sotto pressione, prevenendo difetti come il flash. |
Iniezione | Introduce il materiale fuso nella cavità dello stampo. | Controlla velocità, pressione e temperatura per garantire un riempimento completo e uniforme. |
Raffreddamento | Solidificare il materiale all'interno dello stampo. | Utilizza canali di raffreddamento per evitare deformazioni, ritiri o tensioni interne. |
Espulsione | Rimuovere il pezzo solidificato dallo stampo. | I perni o le piastre di espulsione rilasciano il pezzo senza problemi, evitando graffi o deformazioni. |
Siete pronti a ottimizzare il vostro processo di stampaggio a iniezione? Contattate oggi stesso i nostri esperti per soluzioni su misura!