La macinazione in un mulino a sfere è un processo complesso influenzato da molteplici fattori che determinano l'efficienza, la dimensione delle particelle e le prestazioni complessive del mulino.I fattori chiave includono la velocità di rotazione, le dimensioni e il tipo di mezzo di macinazione, le proprietà del materiale da macinare, il rapporto di riempimento del mulino e i parametri di progettazione del mulino stesso.Questi fattori interagiscono per influenzare il tempo di permanenza, il consumo energetico e la distribuzione granulometrica finale.La comprensione e l'ottimizzazione di queste variabili è fondamentale per ottenere i risultati di macinazione desiderati, sia per la produzione di particelle fini che per la lavorazione efficiente dei materiali.
Punti chiave spiegati:
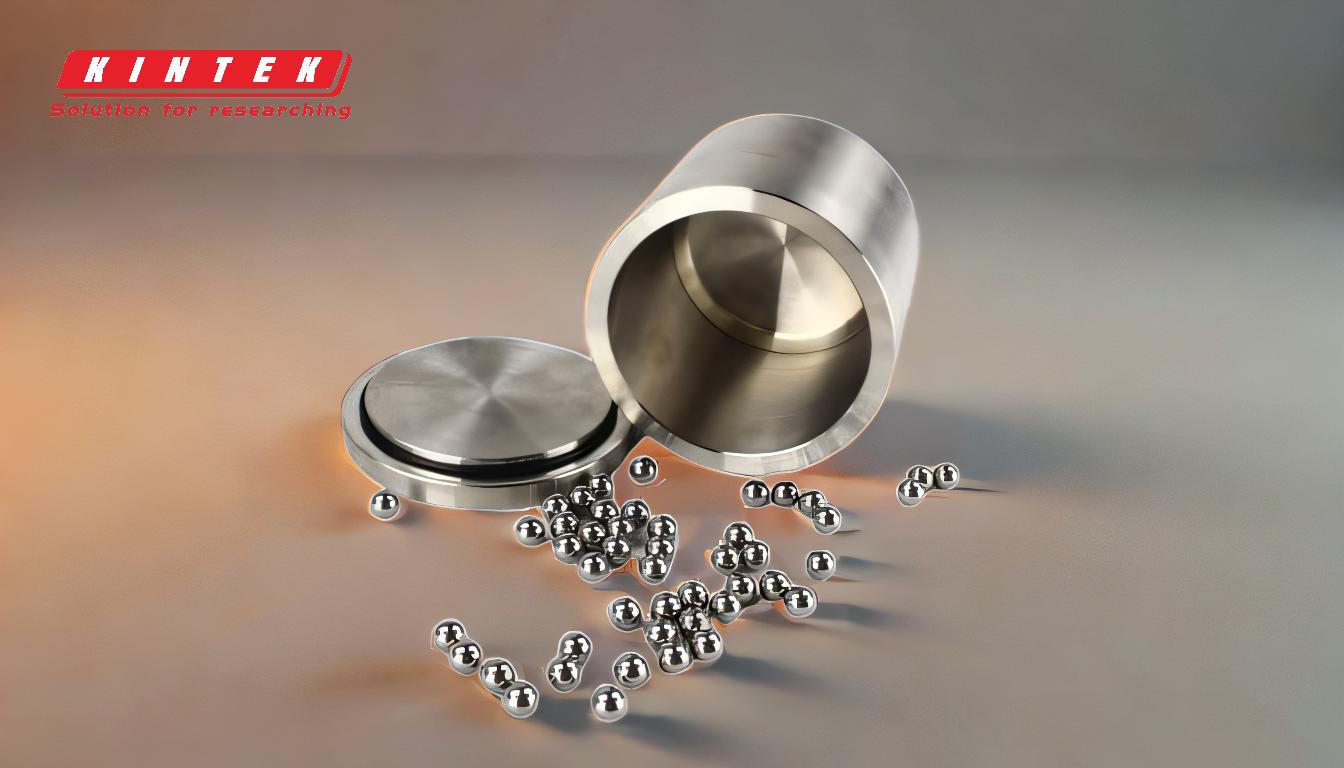
-
Velocità di rotazione
- La velocità di rotazione del mulino a sfere influisce direttamente sul movimento dei mezzi di macinazione e del materiale.
- A velocità ottimali, le sfere vengono sollevate a una certa altezza e poi scendono a cascata, creando forze di impatto e di taglio per la macinazione.
- Se la velocità è troppo bassa, le sfere potrebbero non raggiungere un'altezza sufficiente, riducendo l'efficienza della macinazione.
- Se la velocità è troppo elevata, le sfere possono centrifugare, attaccandosi alle pareti e riducendo l'azione di macinazione.
- La velocità critica (la velocità alla quale avviene la centrifugazione) è un parametro fondamentale da evitare.
-
Dimensione e tipo di mezzo di macinazione
-
La dimensione delle sfere di macinazione influisce sul trasferimento di energia e sulla riduzione delle dimensioni delle particelle.
- Le sfere più grandi sono più efficaci per la macinazione grossolana, mentre quelle più piccole sono migliori per la macinazione fine.
-
La densità e la durezza dei mezzi di macinazione influenzano i tassi di usura e l'efficienza di macinazione.
- I materiali più duri, come l'acciaio o la ceramica, sono preferibili per garantire una durata maggiore e prestazioni costanti.
- Anche il numero di sfere gioca un ruolo importante: un numero troppo basso di sfere riduce l'efficienza della macinazione, mentre un numero eccessivo può portare a un sovraffollamento e a una riduzione dell'energia d'impatto.
-
La dimensione delle sfere di macinazione influisce sul trasferimento di energia e sulla riduzione delle dimensioni delle particelle.
-
Dimensioni e tipo di materiale da macinare
-
La dimensione iniziale delle particelle e la durezza del materiale influiscono in modo significativo sulle prestazioni di macinazione.
- I materiali più duri richiedono più energia e tempo per la macinazione, mentre quelli più morbidi sono più facili da lavorare.
- La velocità di alimentazione e la distribuzione granulometrica del materiale devono essere ottimizzate per evitare di sovraccaricare il mulino o di creare una macinazione non uniforme.
- I materiali con un elevato contenuto di umidità o con proprietà appiccicose possono richiedere aggiustamenti per evitare intasamenti o una riduzione dell'efficienza di macinazione.
-
La dimensione iniziale delle particelle e la durezza del materiale influiscono in modo significativo sulle prestazioni di macinazione.
-
Rapporto di riempimento del mulino
- Il rapporto di riempimento si riferisce alla percentuale del volume del mulino occupata dal mezzo di macinazione.
-
Un rapporto di riempimento ottimale garantisce una macinazione efficiente senza un eccessivo consumo di energia.
- Un rapporto di riempimento troppo basso riduce il numero di impatti di macinazione, diminuendo l'efficienza.
- Un rapporto di riempimento troppo alto può portare a collisioni eccessive tra le sfere, riducendone l'efficacia.
- Il rapporto di riempimento influisce anche sul tempo di permanenza del materiale nel mulino, influenzando la dimensione finale delle particelle.
-
Tempo di permanenza e velocità di alimentazione
-
Il tempo di permanenza è la durata della permanenza del materiale all'interno del mulino, che influisce direttamente sul grado di macinazione.
- Tempi di residenza più lunghi producono generalmente particelle più fini, ma possono ridurre la produttività.
- La velocità di alimentazione deve essere bilanciata con la capacità del mulino per garantire una macinazione costante ed evitare il sovraccarico.
- Per mantenere le condizioni di macinazione ottimali, è necessario un monitoraggio e una regolazione continui della velocità di alimentazione.
-
Il tempo di permanenza è la durata della permanenza del materiale all'interno del mulino, che influisce direttamente sul grado di macinazione.
-
Parametri di progettazione del mulino
-
Il diametro del tamburo e il rapporto lunghezza/diametro (L:D) sono fattori critici di progettazione.
- Un rapporto L:D ottimale (in genere 1,56-1,64) garantisce una macinazione efficiente e l'utilizzo dell'energia.
- La forma e la struttura dell'interno del mulino (superficie della corazza) influenzano il movimento dei mezzi di macinazione e del materiale.
- Una ventilazione adeguata e la rimozione tempestiva del prodotto macinato sono essenziali per evitare il surriscaldamento e mantenere l'efficienza della macinazione.
-
Il diametro del tamburo e il rapporto lunghezza/diametro (L:D) sono fattori critici di progettazione.
-
Proprietà fisico-chimiche del materiale di alimentazione
-
La composizione chimica, la durezza e l'abrasività del materiale influiscono sulle prestazioni di macinazione.
- I materiali abrasivi possono usurare più rapidamente i mezzi di macinazione, richiedendo sostituzioni più frequenti.
- L'area superficiale specifica e la distribuzione granulometrica del materiale macinato sono influenzate dalle proprietà del materiale stesso.
-
La composizione chimica, la durezza e l'abrasività del materiale influiscono sulle prestazioni di macinazione.
-
Numero di cicli di macinazione
- Per ottenere la granulometria desiderata possono essere necessari più cicli di macinazione, soprattutto per la macinazione fine.
- Ogni ciclo aumenta il tempo di permanenza e il consumo energetico, ma migliora l'uniformità del prodotto finale.
-
Fattori ambientali e operativi
- La temperatura e l'umidità possono influire sull'efficienza della macinazione, in particolare per i materiali sensibili all'umidità.
- La corretta manutenzione e l'allineamento del mulino garantiscono prestazioni costanti e riducono i tempi di fermo.
Controllando e ottimizzando attentamente questi fattori, gli operatori possono ottenere processi di macinazione efficienti, ridurre il consumo energetico e produrre materiali macinati di alta qualità con la distribuzione granulometrica desiderata.
Tabella riassuntiva:
Fattore | Impatto |
---|---|
Velocità di rotazione | Influisce sul movimento del mezzo di macinazione; la velocità ottimale garantisce una macinazione efficiente. |
Dimensione/tipo del mezzo di macinazione | Sfere più grandi per la macinazione grossolana, più piccole per la macinazione fine; la durezza del materiale è importante. |
Proprietà del materiale | Durezza, umidità e velocità di avanzamento influenzano l'efficienza di macinazione. |
Rapporto di riempimento | Il rapporto ottimale garantisce una macinazione efficiente senza un eccessivo consumo di energia. |
Tempo di permanenza e velocità di alimentazione | Tempo di residenza più lungo = particelle più fini; una velocità di alimentazione bilanciata evita il sovraccarico. |
Parametri di progettazione del mulino | Il diametro del tamburo, il rapporto L:D e la struttura interna influiscono sull'efficienza di macinazione. |
Fattori ambientali | Temperatura, umidità e manutenzione influiscono sulle prestazioni e sui tempi di inattività. |
Ottimizzate il vostro processo di macinazione a sfere oggi stesso. contattate i nostri esperti per soluzioni su misura!