La dimensione delle particelle influisce in modo significativo sull'efficienza e sui risultati della macinazione a sfere.Le particelle più piccole richiedono generalmente sfere di macinazione più piccole e tempi di macinazione più lunghi per ottenere la finezza desiderata.Il processo è influenzato da diversi fattori, tra cui le dimensioni e il tipo di mezzo di macinazione, le proprietà del materiale da macinare, la velocità di rotazione del mulino e il rapporto di riempimento del mulino.La comprensione di questi fattori aiuta a ottimizzare il processo di macinazione per ottenere una migliore produttività e la distribuzione granulometrica desiderata.
Punti chiave spiegati:
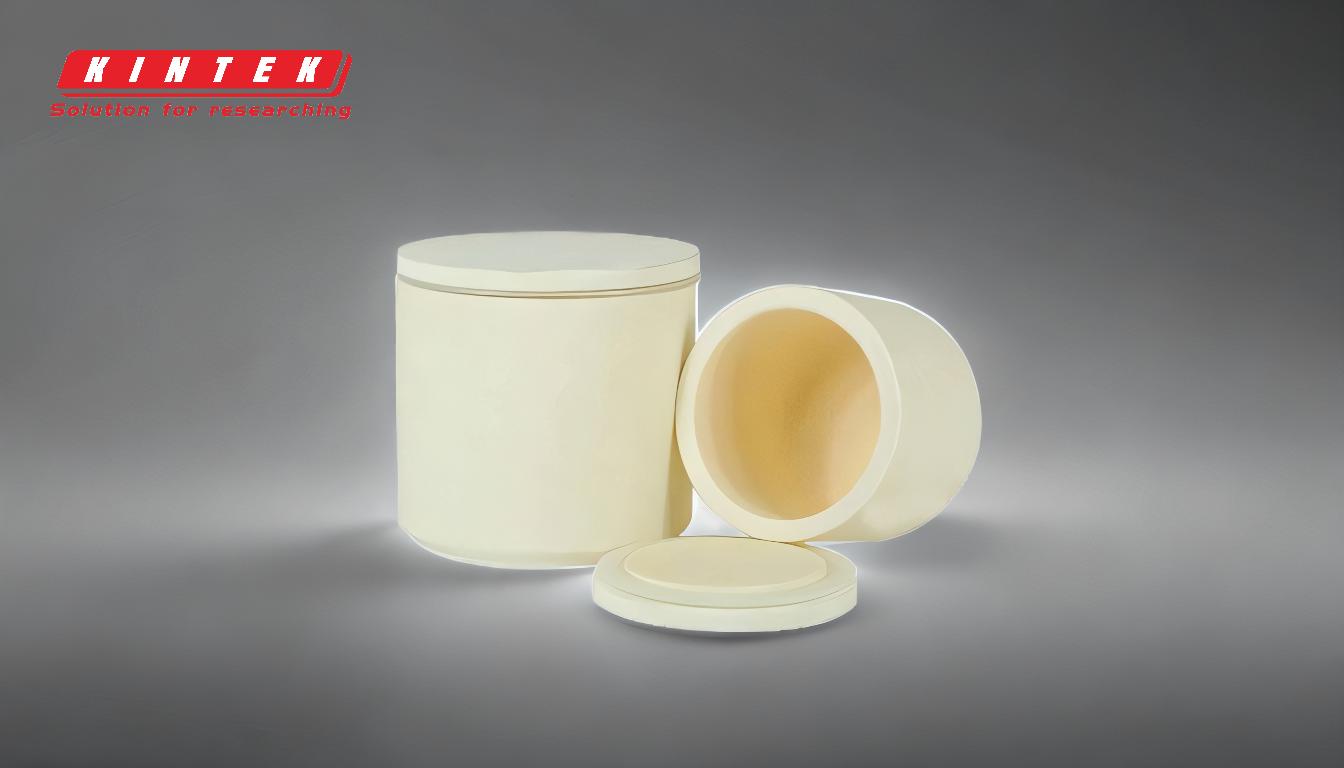
-
Effetto della dimensione della sfera sulla riduzione delle dimensioni delle particelle:
- Palline più piccole:Le sfere di macinazione più piccole sono più efficaci per ridurre le dimensioni delle particelle a livelli più fini.Questo perché le sfere più piccole hanno una superficie maggiore rispetto al loro volume, consentendo un maggior numero di punti di contatto con il materiale da macinare.Questo maggiore contatto aumenta l'efficienza della macinazione, soprattutto per ottenere particelle di dimensioni ridotte.
- Sfere più grandi:Le sfere più grandi sono in genere utilizzate per la macinazione più grossolana.Sono più efficaci nel rompere le particelle più grandi, ma potrebbero non essere altrettanto efficienti per la macinazione fine, a causa del minor numero di punti di contatto e della minore area superficiale.
-
Impatto del tempo di macinazione:
- Tempi di fresatura più lunghi:L'ottenimento di particelle di dimensioni ridotte richiede spesso tempi di macinazione più lunghi.Una macinazione prolungata consente un maggior numero di collisioni tra le sfere di macinazione e il materiale, con conseguenti dimensioni delle particelle più fini.Tuttavia, tempi di macinazione troppo lunghi possono portare a una macinazione eccessiva, che potrebbe non essere auspicabile per alcuni materiali.
- Tempi di fresatura più brevi:Tempi di macinazione più brevi sono generalmente sufficienti per una macinazione più grossolana, ma potrebbero non essere adeguati per ottenere particelle molto fini.
-
Influenza della velocità di rotazione del mulino:
- Velocità ottimale:La velocità di rotazione del mulino influisce sull'energia cinetica delle sfere di macinazione.Una velocità ottimale garantisce che le sfere vengano sollevate a una certa altezza prima di cadere, creando forze di impatto e di taglio che macinano il materiale.Una velocità troppo elevata può causare la centrifugazione delle sfere, riducendo l'efficienza della macinazione, mentre una velocità troppo bassa può non fornire energia sufficiente per una macinazione efficace.
-
Ruolo del rapporto di riempimento del mulino:
- Rapporto di riempimento:La percentuale del volume del mulino riempito con il mezzo di macinazione (sfere) influisce sull'efficienza di macinazione.Un rapporto di riempimento ottimale garantisce la presenza di un numero sufficiente di sfere per macinare efficacemente il materiale senza sovraffollamento, che può ridurre l'efficienza del processo di macinazione.
-
Proprietà del materiale:
- Durezza e natura del materiale:La durezza e la natura del materiale da macinare giocano un ruolo fondamentale nel determinare l'efficienza della macinazione.I materiali più duri possono richiedere più energia e tempo per ottenere le dimensioni desiderate delle particelle, mentre quelli più morbidi possono macinare più facilmente.
-
Tempo di permanenza e velocità di alimentazione:
- Tempo di permanenza:Il tempo che il materiale trascorre nella camera del mulino influisce sul grado di macinazione.Tempi di permanenza più lunghi consentono una macinazione più accurata, che porta a particelle più fini.
- Velocità di alimentazione:Anche la velocità di alimentazione del materiale nel mulino influisce sul processo di macinazione.Una velocità di alimentazione costante e appropriata assicura che il materiale venga macinato in modo uniforme ed efficiente.
-
Design e dimensioni del mulino:
- Diametro e lunghezza del tamburo:Le dimensioni del mulino, in particolare il diametro del tamburo e il rapporto tra diametro e lunghezza, influenzano le prestazioni di macinazione.Un rapporto L:D ottimale (in genere 1,56-1,64) garantisce una macinazione efficiente e la produttività.
- Forma della superficie della corazza:La forma della superficie interna del mulino può influire sul movimento delle sfere di macinazione e sul materiale, influenzando l'efficienza di macinazione.
-
Considerazioni sulla produttività:
- Finezza di macinazione:La finezza desiderata del prodotto macinato influisce sulla produttività complessiva del mulino.Una macinazione più fine richiede in genere più tempo ed energia, il che può ridurre la produttività.
- Rimozione tempestiva del prodotto macinato:La rimozione efficiente del prodotto macinato dal mulino è fondamentale per mantenere la produttività.Una rimozione ritardata può portare a una macinazione eccessiva e a una riduzione dell'efficienza.
In sintesi, la dimensione delle particelle nella macinazione a sfere è influenzata da una combinazione di fattori, tra cui la dimensione della sfera, il tempo di macinazione, la velocità di rotazione, il rapporto di riempimento del mulino, le proprietà del materiale, il tempo di residenza, la velocità di alimentazione e il design del mulino.L'ottimizzazione di questi fattori può aiutare a ottenere la distribuzione granulometrica desiderata e a migliorare l'efficienza complessiva del processo di macinazione.
Tabella riassuntiva:
Fattore | Impatto sulla macinazione a sfere |
---|---|
Dimensione delle sfere | Sfere più piccole per la macinazione fine; sfere più grandi per la macinazione grossolana. |
Tempo di macinazione | Tempi più lunghi per particelle più fini; tempi più brevi per risultati più grossolani. |
Velocità di rotazione | La velocità ottimale garantisce una macinazione efficiente; velocità troppo alte o basse riducono l'efficienza. |
Rapporto di riempimento del mulino | Il rapporto di riempimento ottimale massimizza l'efficienza di macinazione senza sovraffollamento. |
Proprietà del materiale | La durezza e la natura del materiale influiscono sul tempo di macinazione e sui requisiti energetici. |
Tempo di residenza | Tempi di residenza più lunghi portano a particelle più fini. |
Velocità di alimentazione | Una velocità di alimentazione costante garantisce una macinazione uniforme ed efficiente. |
Design del mulino | Il diametro, la lunghezza e la forma interna del tamburo influenzano le prestazioni di macinazione. |
Produttività | Una macinazione più fine riduce la produttività; la rimozione tempestiva del prodotto macinato mantiene l'efficienza. |
Siete pronti a ottimizzare il vostro processo di macinazione a sfere? Contattate i nostri esperti oggi stesso per soluzioni su misura!