Gli elementi riscaldanti possono smettere di funzionare per una serie di motivi, che vanno dal degrado fisico ai problemi operativi.Le cause principali includono la formazione di punti caldi, l'ossidazione dovuta al funzionamento intermittente, l'infragilimento dovuto alla crescita dei grani e la contaminazione o la corrosione.Inoltre, problemi elettrici come interruttori scattati, fusibili bruciati o interruttori difettosi possono impedire all'alimentazione di raggiungere l'elemento riscaldante, rendendolo non funzionante.La comprensione di questi meccanismi di guasto è fondamentale per mantenere la longevità e l'efficienza degli elementi riscaldanti in varie applicazioni.
Punti chiave spiegati:
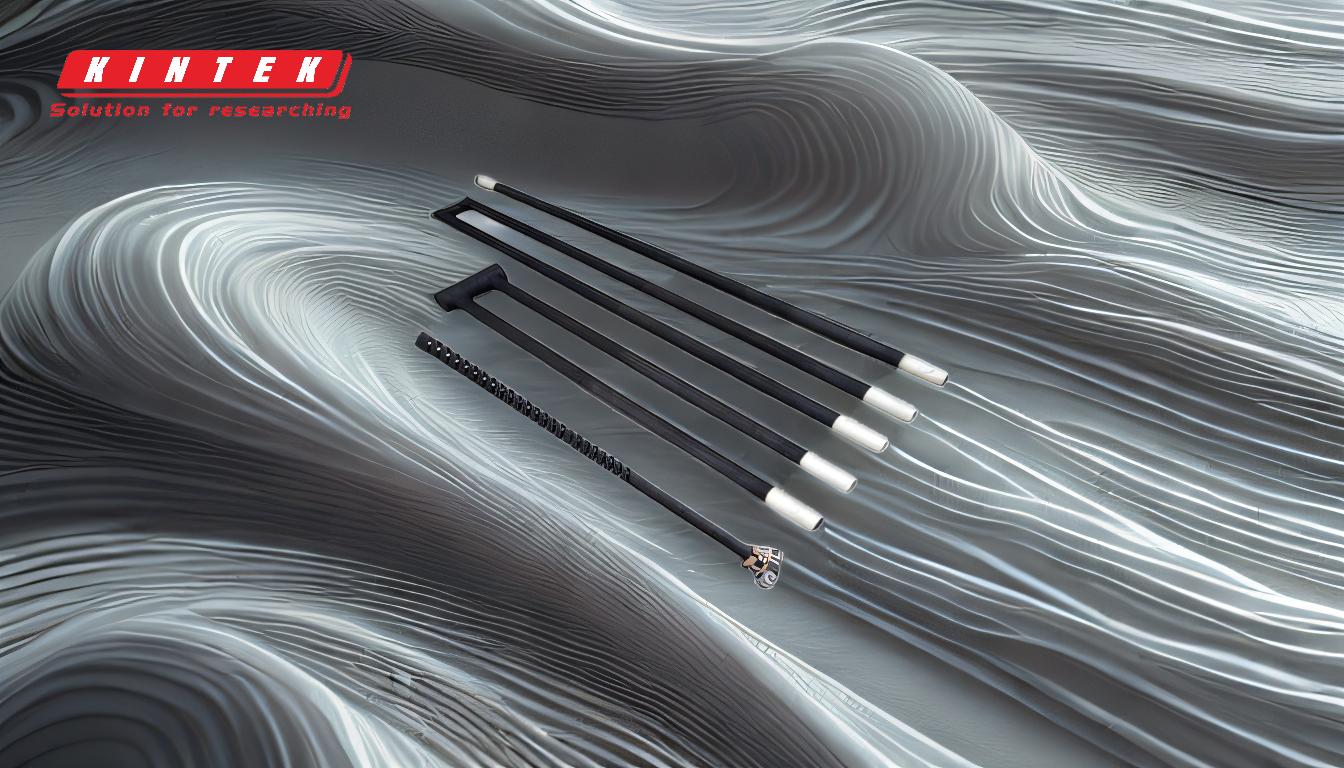
-
Formazione di punti caldi
- Descrizione:I punti caldi si verificano quando alcune aree dell'elemento riscaldante diventano significativamente più calde rispetto al resto.Ciò può essere dovuto a un'elevata ossidazione locale o alla schermatura da parte dei supporti.
- Impatto:Queste temperature elevate localizzate possono portare a una degradazione accelerata e a un eventuale guasto dell'elemento riscaldante.
- Prevenzione:Un riscaldamento uniforme e un corretto posizionamento del supporto possono contribuire a ridurre la formazione di punti caldi.
-
Ossidazione e intermittenza del funzionamento
- Descrizione:I frequenti cicli di riscaldamento e raffreddamento fanno sì che lo strato di ossido sull'elemento riscaldante si rompa e si sfaldi, esponendo il metallo fresco a un'ulteriore ossidazione.
- Impatto:Questo processo indebolisce l'elemento nel tempo, portandolo al cedimento.
- Prevenzione:Riducendo al minimo i rapidi sbalzi di temperatura e utilizzando materiali con una migliore resistenza all'ossidazione si può prolungare la durata dell'elemento.
-
Infragilimento dovuto alla crescita dei grani
- Descrizione:Le leghe riscaldanti, soprattutto quelle contenenti ferro, possono formare grani grandi e fragili alle alte temperature.
- Impatto:L'infragilimento rende l'elemento più suscettibile alla fessurazione e alla rottura sotto sforzo.
- Prevenzione:L'utilizzo di leghe progettate per resistere alla crescita dei grani e il mantenimento di temperature di esercizio ottimali possono aiutare a prevenire l'infragilimento.
-
Contaminazione e corrosione
- Descrizione:L'esposizione a gas o fumi corrosivi nell'ambiente del forno può contaminare gli elementi riscaldanti, provocando la corrosione a secco.
- Impatto:La contaminazione e la corrosione degradano il materiale, riducendone l'efficacia e portandolo al fallimento.
- Prevenzione:L'implementazione di una ventilazione adeguata e l'utilizzo di materiali resistenti alla corrosione possono proteggere gli elementi dalla contaminazione.
-
Problemi elettrici
- Descrizione:Problemi di alimentazione, come interruttori scattati, fusibili bruciati o interruttori difettosi, possono impedire all'elemento riscaldante di ricevere energia.
- Impatto:Senza alimentazione, l'elemento riscaldante non può funzionare, indipendentemente dalle sue condizioni fisiche.
- Prevenzione:Controlli regolari di manutenzione dell'impianto elettrico e la sostituzione immediata dei componenti difettosi possono garantire un'alimentazione costante.
Affrontando questi punti chiave, gli utenti possono comprendere meglio le potenziali modalità di guasto degli elementi riscaldanti e adottare misure proattive per prevenirle, garantendo un funzionamento affidabile ed efficiente a lungo termine.
Tabella riassuntiva:
Causa del guasto | Descrizione | Impatto | Prevenzione |
---|---|---|---|
Formazione di punti caldi | Elevate temperature localizzate dovute all'ossidazione o alla schermatura da parte dei supporti. | Accelerazione del degrado e guasto. | Assicurare un riscaldamento uniforme e un corretto posizionamento del supporto. |
Ossidazione | I frequenti cicli di riscaldamento/raffreddamento incrinano lo strato di ossido, esponendo il metallo fresco. | L'elemento si indebolisce nel tempo. | Ridurre al minimo i rapidi sbalzi di temperatura; utilizzare materiali resistenti all'ossidazione. |
Infragilimento | Nelle leghe riscaldate ad alte temperature si formano grani grandi e fragili. | Aumenta la suscettibilità alle cricche e alle rotture. | Utilizzare leghe resistenti alla crescita dei grani; mantenere temperature di esercizio ottimali. |
Contaminazione/Corrosione | L'esposizione a gas o fumi corrosivi contamina l'elemento. | Degrado del materiale e guasto. | Implementare una ventilazione adeguata; utilizzare materiali resistenti alla corrosione. |
Problemi elettrici | Interruttori scattati, fusibili bruciati o interruttori difettosi impediscono l'alimentazione. | L'elemento riscaldante non può funzionare senza alimentazione. | Eseguire controlli regolari dell'impianto elettrico; sostituire tempestivamente i componenti difettosi. |
Avete bisogno di aiuto per la manutenzione o la sostituzione degli elementi di riscaldamento? Contattate i nostri esperti oggi stesso per soluzioni su misura!