L'ossido di zirconio (zirconia) si sinterizza tipicamente a temperature elevate, comprese tra 1400°C e 1600°C, con la maggior parte dei processi che si avvicinano a 1500°C - 1550°C.Questo intervallo di temperature è fondamentale per ottenere la durezza, la densità e la resistenza desiderate del prodotto finale.La sinterizzazione a queste temperature trasforma l'ossido di zirconio da una struttura monoclina a una politetragonale, migliorandone significativamente le proprietà meccaniche.Tuttavia, deviazioni da questo intervallo ottimale, anche di 150°C, possono portare a una riduzione della resistenza a causa della crescita dei grani.Per questo processo sono necessari forni specializzati per la sinterizzazione ad alta temperatura, poiché i forni per porcellana standard non possono raggiungere queste temperature.
Punti chiave spiegati:
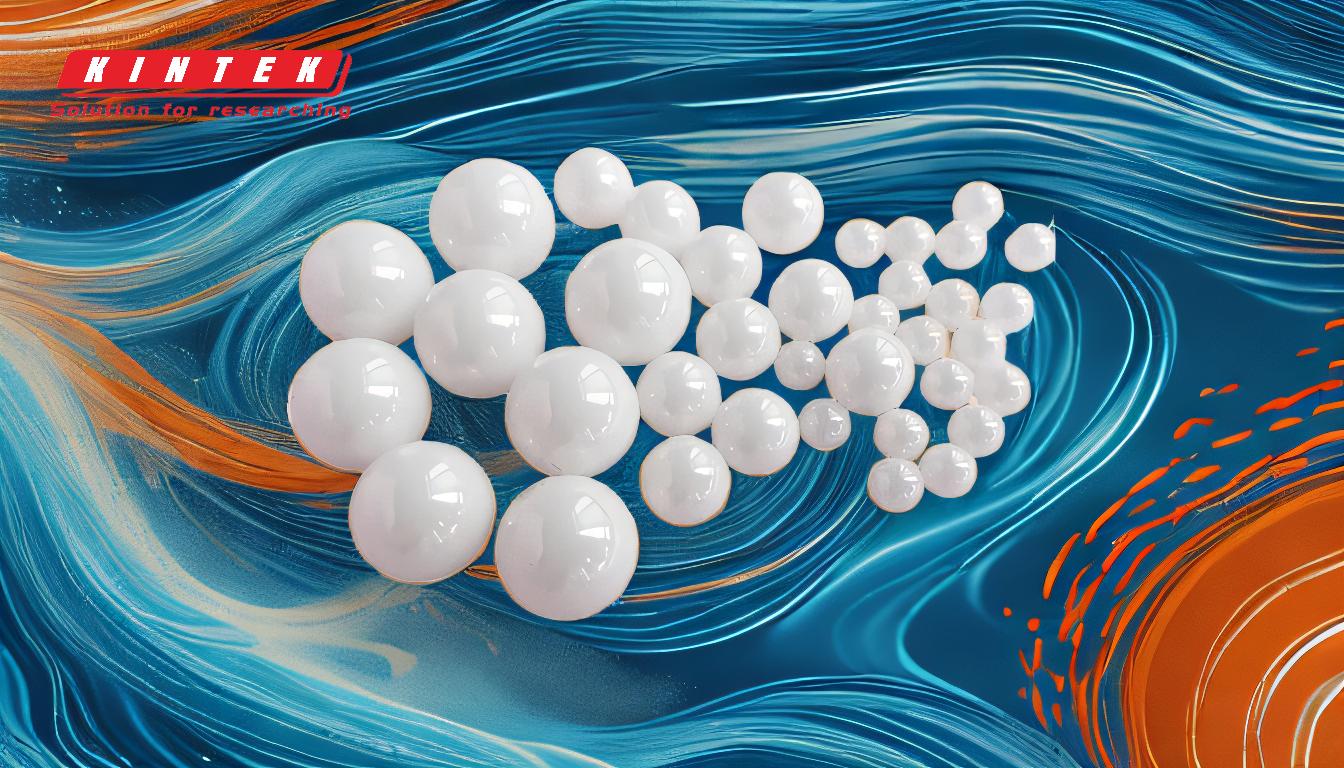
-
Intervallo ottimale di temperatura di sinterizzazione:
- La zirconia si sinterizza efficacemente tra 1400°C e 1600°C con la maggior parte dei processi che mirano a 1500°C - 1550°C .
- Questo intervallo garantisce la trasformazione della struttura cristallina da monoclina a politetragonale, essenziale per ottenere densità e resistenza elevate.
- La sinterizzazione a queste temperature fa sì che l'ossido di zirconio raggiunga quasi il 99% della sua densità massima teorica .
-
Impatto della temperatura sulla resistenza:
- Cottura dell'ossido di zirconio a 1500°C a 1550°C produce la massima resistenza, con valori intorno a 1280 MPa .
-
Se ci si discosta da questo intervallo di
±150°C
può ridurre significativamente la resistenza:
- A 1600°C la resistenza scende a circa 980 MPa .
- A 1700°C la resistenza diminuisce ulteriormente fino a circa 600 MPa .
- Questa riduzione della resistenza è attribuita all'eccessiva crescita dei grani alle temperature più elevate.
-
Tasso di aumento del calore:
- Un lento aumento di calore di 4°C a 10°C al minuto durante la sinterizzazione.
- Questo riscaldamento controllato assicura una densificazione uniforme e riduce al minimo le tensioni interne, che altrimenti potrebbero causare difetti nel prodotto finale.
-
Requisiti del forno:
- Specializzati forni di sinterizzazione ad alta temperatura sono necessari per la lavorazione della zirconia.
- I forni per porcellana standard, tipicamente utilizzati per la cottura per infiltrazione del vetro, non possono raggiungere le alte temperature necessarie per la sinterizzazione della zirconia.
-
Trasformazione strutturale:
- La trasformazione da zircone monoclino a zircone politetragonale avviene a 1100°C a 1200°C .
- Tuttavia, per ottenere una densificazione completa e proprietà meccaniche ottimali è necessario sinterizzare a temperature più elevate ( 1400°C - 1600°C ).
-
Considerazioni pratiche per gli acquirenti:
- Quando si sceglie un forno di sinterizzazione, assicurarsi che sia in grado di mantenere costantemente temperature comprese tra i 1500°C a 1550°C gamma.
- Verificare l'accuratezza e l'uniformità della temperatura del forno, poiché piccole deviazioni possono influire sulla resistenza del prodotto finale.
- Considerare forni con tassi di aumento del calore programmabili per raggiungere i valori raccomandati di da 4°C a 10°C al minuto profilo di riscaldamento.
Attenendosi a queste linee guida, gli acquirenti possono garantire la produzione di componenti in zirconia di alta qualità con proprietà meccaniche ottimali.
Tabella riassuntiva:
Fattore chiave | Dettagli |
---|---|
Intervallo di sinterizzazione ottimale | 1400°C-1600°C (obiettivo 1500°C-1550°C) |
Resistenza a 1500°C-1550°C | ~1280 MPa |
Riduzione della resistenza a 1600°C | ~980 MPa |
Riduzione della resistenza a 1700°C | ~600 MPa |
Velocità di aumento del calore | 4°C-10°C al minuto |
Tipo di forno | Forno specializzato per la sinterizzazione ad alta temperatura (i forni standard per la porcellana sono insufficienti) |
Densità raggiunta | ~99% del massimo teorico |
Trasformazione strutturale | Da monoclino a politetragonale a 1100°C-1200°C |
Assicuratevi che il vostro processo di sinterizzazione dell'ossido di zirconio sia conforme agli standard del settore. contattate oggi i nostri esperti per soluzioni su misura!