La riduzione dimensionale massima in un mulino a sfere è influenzata da una combinazione di fattori, tra cui la velocità di rotazione, le dimensioni e il tipo di mezzo di macinazione, la natura del materiale da macinare e i parametri operativi del mulino.La riduzione dimensionale ottimale si verifica quando il mulino funziona a velocità normale, consentendo alle sfere di muoversi in cascata e di colpire efficacemente il materiale.Per ottenere particelle di dimensioni più fini sono generalmente necessarie sfere più piccole e tempi di macinazione più lunghi.L'efficienza della riduzione dimensionale è influenzata anche dal rapporto di riempimento del mulino, dalla durezza del materiale e dalle proprietà fisico-chimiche del materiale di alimentazione.La comprensione di questi fattori è fondamentale per ottenere le dimensioni desiderate delle particelle e massimizzare le prestazioni di macinazione di un mulino a sfere.
Punti chiave spiegati:
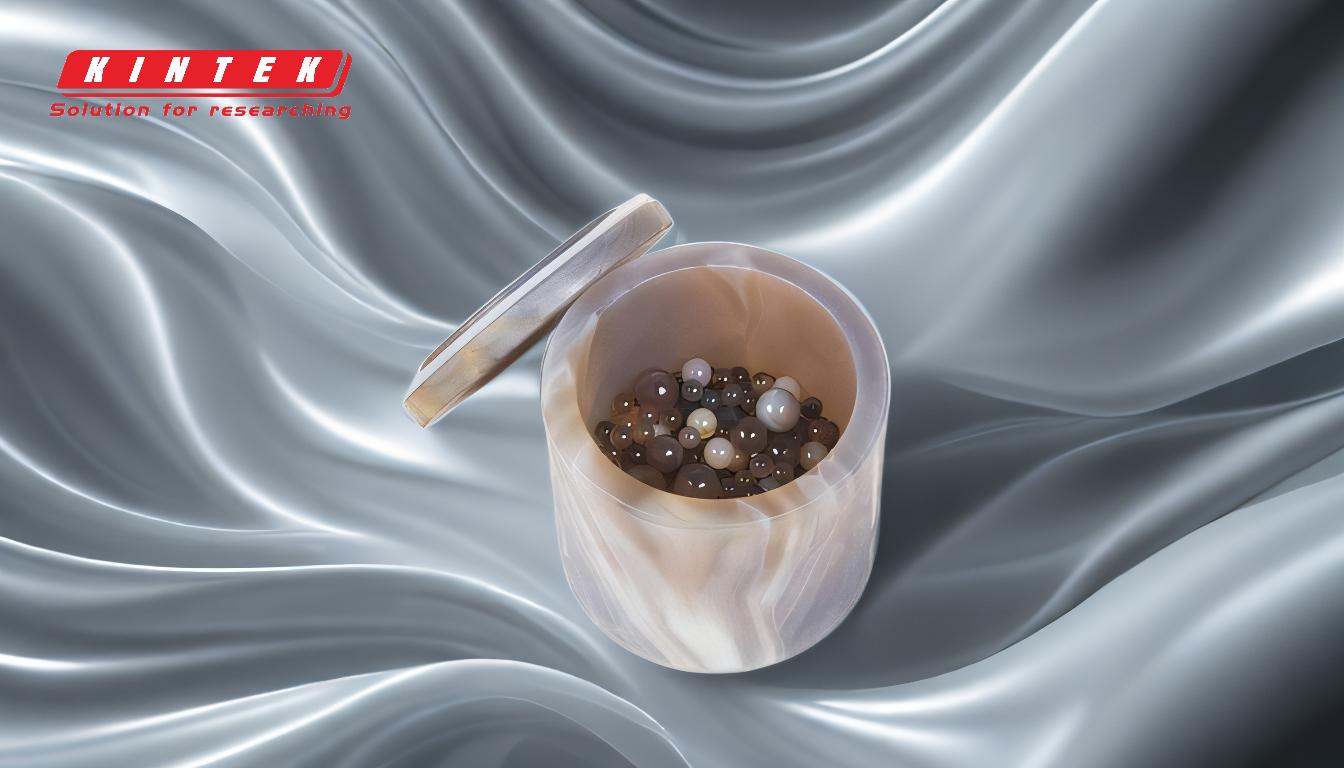
-
Velocità di rotazione:
- La velocità di rotazione del mulino a sfere svolge un ruolo fondamentale nella riduzione delle dimensioni.
- Bassa velocità:A bassa velocità, le sfere tendono a scivolare o a rotolare l'una sull'altra, riducendo al minimo le dimensioni.
- Alta velocità:A velocità elevate, le sfere vengono scagliate contro la parete del cilindro a causa della forza centrifuga, impedendo una macinazione efficace.
- Velocità normale:A velocità normali, le sfere vengono portate in cima al mulino e poi scendono a cascata, impattando il materiale e ottenendo la massima riduzione dimensionale.
-
Mezzo di macinazione:
- Le dimensioni, la densità e il numero di sfere utilizzate nel mulino influiscono in modo significativo sull'efficienza di macinazione.
- Sfere più piccole:Le sfere più piccole sono generalmente più efficaci nel produrre particelle più fini perché hanno una superficie maggiore rispetto al loro volume, consentendo un maggior numero di punti di contatto con il materiale.
- Densità e numero:Anche la densità e il numero di sfere influenzano il trasferimento di energia durante la macinazione.Le sfere a densità più elevata possono imprimere più energia al materiale, mentre un numero maggiore di sfere aumenta la frequenza degli impatti.
-
Natura del materiale:
- La durezza e le proprietà fisico-chimiche del materiale da macinare sono fattori cruciali.
- Durezza:I materiali più duri richiedono una maggiore energia per la frantumazione, che può essere ottenuta utilizzando sfere più dense o aumentando il tempo di macinazione.
- Proprietà fisico-chimiche:Le proprietà del materiale, come la fragilità o la tenacità, possono influire sulla facilità di rottura in caso di impatto.
-
Parametri operativi:
- Diversi parametri operativi influenzano le prestazioni di macinazione, tra cui la velocità di alimentazione, il tempo di permanenza e il rapporto di riempimento.
- Velocità di alimentazione:La velocità di alimentazione del materiale nel mulino influisce sul tempo di permanenza e sul grado di macinazione.Una velocità di alimentazione più elevata può ridurre il tempo di residenza, portando a una macinazione meno efficace.
- Tempo di residenza:I tempi di permanenza più lunghi consentono una macinazione più accurata, soprattutto quando si punta a ottenere particelle di dimensioni più fini.
- Rapporto di riempimento:La percentuale del volume del mulino riempito con il mezzo di macinazione (sfere) influisce sull'efficienza del processo di macinazione.Un rapporto di riempimento ottimale assicura che ci sia spazio sufficiente per le sfere per muoversi in cascata e colpire il materiale in modo efficace.
-
Design del mulino:
- Anche il design del mulino a sfere, compreso il diametro del tamburo e il rapporto tra diametro e lunghezza del tamburo, influisce sulla riduzione delle dimensioni.
- Diametro del tamburo:I diametri più grandi del tamburo possono ospitare un maggior numero di sfere e fornire una maggiore superficie di macinazione.
- Rapporto L:D:Il rapporto ottimale tra lunghezza e diametro (L:D) per un mulino a sfere è in genere compreso tra 1,56 e 1,64. Questo rapporto garantisce che il materiale venga macinato adeguatamente senza un eccessivo consumo di energia.Questo rapporto garantisce un'adeguata macinazione del materiale senza un eccessivo consumo di energia.
-
Tempo di macinazione:
- La durata della macinazione è direttamente correlata al grado di riduzione delle dimensioni.
- Tempi di macinazione più lunghi:Per ottenere particelle di dimensioni più fini sono generalmente necessari tempi di macinazione più lunghi, poiché il materiale subisce più impatti e abrasioni nel tempo.
-
Rimozione tempestiva del prodotto macinato:
- Una rimozione efficiente del prodotto macinato dal mulino è essenziale per evitare una macinazione eccessiva e per mantenere la distribuzione granulometrica desiderata.
- Sovramacinazione:Se il prodotto macinato non viene rimosso tempestivamente, può continuare a essere macinato, causando un eccesso di fini e uno spreco di energia.
In sintesi, la massima riduzione dimensionale in un mulino a sfere è una complessa interazione di fattori, tra cui la velocità di rotazione, le caratteristiche del mezzo di macinazione, le proprietà del materiale, i parametri operativi, il design del mulino e il tempo di macinazione.La comprensione e l'ottimizzazione di questi fattori sono essenziali per ottenere le dimensioni desiderate delle particelle e massimizzare l'efficienza del processo di macinazione.
Tabella riassuntiva:
Fattore | Impatto sulla riduzione delle dimensioni |
---|---|
Velocità di rotazione | La velocità normale garantisce una cascata di sfere efficace, massimizzando l'impatto e la riduzione delle dimensioni. |
Macinazione media | Le sfere più piccole e la maggiore densità migliorano l'efficienza di macinazione per le particelle più fini. |
Natura del materiale | I materiali più duri richiedono più energia; la fragilità influisce sulla frattura in caso di impatto. |
Parametri operativi | La velocità di alimentazione, il tempo di permanenza e il rapporto di riempimento influenzano l'efficienza di macinazione e la dimensione delle particelle. |
Progettazione del mulino | Il diametro ottimale del tamburo e il rapporto L:D garantiscono una macinazione efficace senza un eccessivo consumo di energia. |
Tempo di macinazione | Per le particelle più fini sono necessari tempi di macinazione più lunghi. |
Rimozione del prodotto | La rimozione tempestiva previene la macinazione eccessiva e mantiene la distribuzione granulometrica desiderata. |
Ottimizzate le prestazioni del vostro mulino a sfere contattate oggi i nostri esperti per soluzioni su misura!