I rivestimenti in carbonio simile al diamante (DLC) sono ampiamente riconosciuti per le loro eccellenti proprietà, come l'elevata durezza, il basso attrito e la resistenza all'usura.Tuttavia, presentano anche diversi svantaggi che possono limitarne l'applicabilità in determinati scenari.Tra questi, le sfide legate ai processi di deposizione, alla compatibilità dei materiali e alle prestazioni in condizioni specifiche.La comprensione di questi limiti è fondamentale per prendere decisioni informate quando si considerano i rivestimenti DLC per varie applicazioni.
Punti chiave spiegati:
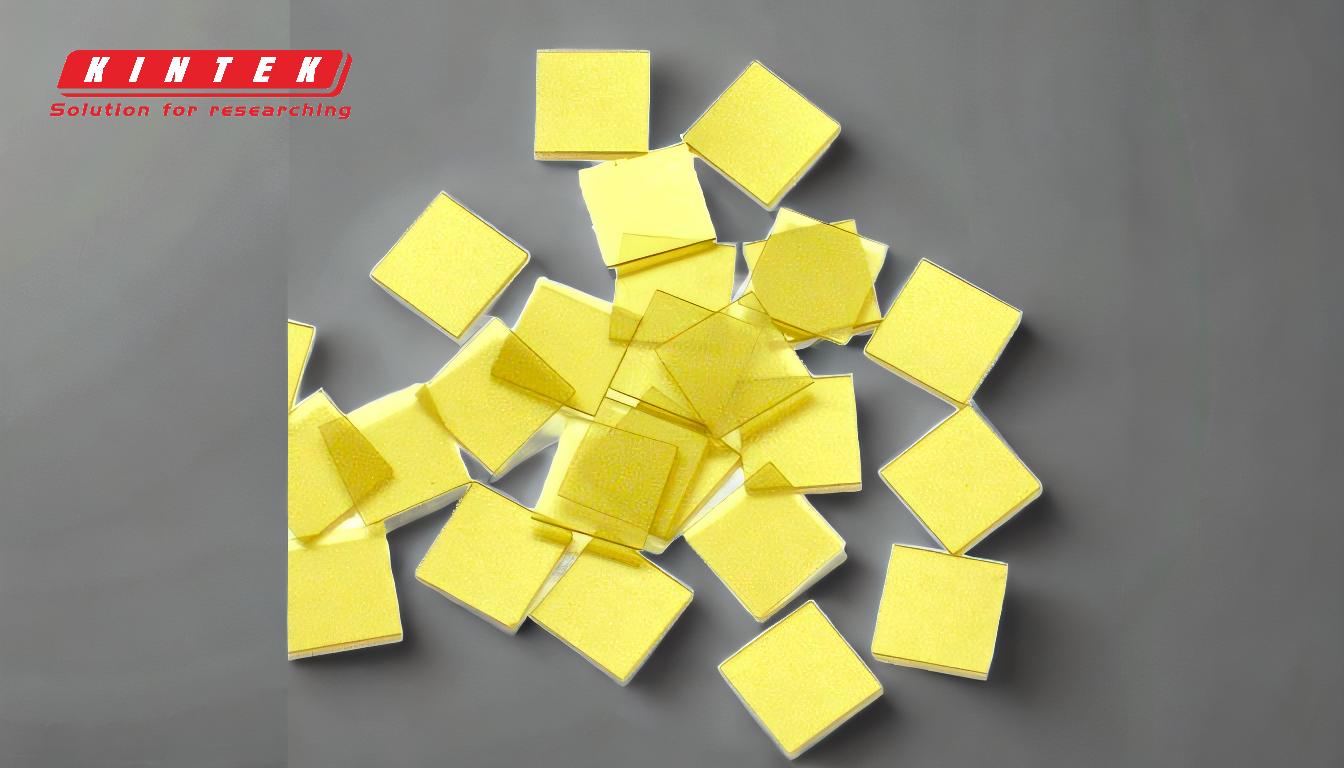
-
Limitazioni del processo di deposizione:
- Temperature di lavorazione elevate:I rivestimenti DLC, in particolare quelli applicati tramite deposizione chimica da vapore (CVD), richiedono spesso temperature di lavorazione elevate (800-1000 °C).Questo limita il loro utilizzo a materiali che possono sopportare tale calore, come il carburo cementato.Molti materiali, in particolare i polimeri e alcuni metalli, non possono sopportare queste temperature, limitando così la gamma di applicazioni.
- Difficoltà di mascheratura:I rivestimenti CVD sono difficili da mascherare, e spesso danno luogo a un rivestimento che non ha nulla da invidiare a nessuno.Ciò significa che il rivestimento selettivo di aree specifiche è difficile da realizzare, il che può rappresentare uno svantaggio significativo quando è necessario rivestire solo alcune parti di un componente.
- Vincoli dimensionali:Le dimensioni dei pezzi che possono essere rivestiti sono limitate dalla capacità della camera di reazione.I componenti grandi o complessi possono dover essere suddivisi in parti più piccole, complicando il processo e aumentando i costi.
-
Spessore del rivestimento e problemi di stress:
- Rivestimenti spessi e sollecitazioni di trazione:I rivestimenti DLC, soprattutto quelli applicati tramite CVD, possono essere relativamente spessi (10-20 μm).Durante il raffreddamento, questi rivestimenti spessi possono generare tensioni di trazione che portano alla formazione di sottili cricche.Queste cricche possono propagarsi in caso di impatto esterno, causando il distacco del rivestimento.Ciò rende i rivestimenti DLC meno adatti alle applicazioni che prevedono processi di taglio interrotti, come la fresatura, dove il rivestimento è più soggetto a cedimenti.
- Sfide di adesione:L'adesione dei rivestimenti DLC a determinati substrati può essere problematica, soprattutto se il materiale del substrato non è compatibile con le alte temperature o se la preparazione della superficie è inadeguata.Una scarsa adesione può portare alla delaminazione e alla riduzione delle prestazioni del rivestimento.
-
Limitazioni delle prestazioni in condizioni specifiche:
- Processi di taglio interrotti:I rivestimenti DLC non sono ideali per i processi di taglio interrotti come la fresatura.Gli urti e i cicli termici ripetuti in questi processi possono esacerbare la formazione di cricche e portare alla rottura del rivestimento.Ciò ne limita l'uso in alcune applicazioni di lavorazione dove altri rivestimenti potrebbero avere prestazioni migliori.
- Contenuto di idrogeno e stabilità:Alcuni rivestimenti DLC contengono idrogeno, che può influire sulla loro stabilità e sulle loro prestazioni, soprattutto a temperature elevate.I rivestimenti DLC idrogenati possono degradarsi o perdere le loro proprietà se esposti a temperature elevate, limitandone l'uso in applicazioni ad alta temperatura.
-
Costo e complessità:
- Costo elevato della deposizione:Le apparecchiature e i processi necessari per depositare i rivestimenti DLC, in particolare tramite CVD, sono complessi e costosi.Ciò può rendere i rivestimenti DLC proibitivi dal punto di vista dei costi per alcune applicazioni, soprattutto se confrontati con rivestimenti alternativi.
- Complessità del processo:La necessità di temperature elevate, di attrezzature specializzate e di un controllo preciso dei parametri di deposizione aumenta la complessità del processo.Ciò può aumentare i tempi e i costi di produzione, rendendo i rivestimenti DLC meno interessanti per le applicazioni ad alto volume o a basso costo.
-
Compatibilità dei materiali e campo di applicazione:
- Compatibilità limitata con i substrati:I rivestimenti DLC non sono universalmente compatibili con tutti i materiali.Ad esempio, possono non aderire bene ad alcuni metalli o polimeri, limitandone l'uso in applicazioni in cui questi materiali sono prevalenti.
- Campo di applicazione limitato:A causa delle limitazioni sopra menzionate, i rivestimenti DLC sono spesso limitati ad applicazioni specifiche in cui le loro proprietà uniche, come il basso attrito e l'elevata resistenza all'usura, sono essenziali.In altri casi, rivestimenti alternativi potrebbero essere più adatti.
In sintesi, i rivestimenti DLC offrono vantaggi significativi in termini di durezza, riduzione dell'attrito e resistenza all'usura, ma presentano anche notevoli svantaggi.Tra questi, le sfide legate al processo di deposizione, allo spessore e alle sollecitazioni del rivestimento, alle prestazioni in condizioni specifiche, ai costi e alla compatibilità dei materiali.La comprensione di queste limitazioni è fondamentale per selezionare il rivestimento appropriato per una determinata applicazione e garantire prestazioni e durata ottimali.
Tabella riassuntiva:
Svantaggio | Descrizione |
---|---|
Elevate temperature di lavorazione | Richiede 800-1000 °C, limitando l'uso a materiali resistenti al calore. |
Difficoltà di mascheratura | Il rivestimento selettivo è impegnativo; spesso si ottiene un'applicazione "tutto o niente". |
Vincoli dimensionali | Limitato dalle dimensioni della camera di reazione, che complica i componenti grandi o complessi. |
Rivestimenti spessi e sollecitazioni di trazione | I rivestimenti spessi (10-20 μm) possono rompersi sotto sforzo, provocando il distacco. |
Problemi di adesione | La scarsa adesione a determinati substrati può causare delaminazione. |
Processi di taglio interrotti | Non è ideale per la fresatura a causa della formazione di cricche in seguito a impatti ripetuti. |
Contenuto di idrogeno e stabilità | I rivestimenti idrogenati possono degradarsi alle alte temperature. |
Costo elevato della deposizione | Attrezzature complesse e costose aumentano i costi complessivi. |
Compatibilità limitata con i substrati | Non è universalmente compatibile con tutti i materiali e limita la gamma di applicazioni. |
Avete bisogno di aiuto per scegliere il rivestimento giusto per la vostra applicazione? Contattate i nostri esperti oggi stesso !