L'aumento della produzione di un mulino a sfere comporta l'ottimizzazione di vari fattori che influenzano le prestazioni di macinazione.I fattori chiave includono la velocità di rotazione, le dimensioni e il tipo di mezzo di macinazione, le proprietà del materiale, il rapporto di riempimento del mulino e i parametri operativi come la velocità di alimentazione e il tempo di permanenza.Regolando attentamente queste variabili, è possibile migliorare l'efficienza e la resa del mulino a sfere.Ciò comporta la scelta della dimensione e della densità delle sfere, il mantenimento di un rapporto L:D ottimale, la rimozione tempestiva del prodotto macinato e il bilanciamento della velocità di alimentazione con la capacità di macinazione.Di seguito analizziamo in dettaglio questi fattori per fornire una comprensione completa di come aumentare la produzione in un mulino a sfere.
Punti chiave spiegati:
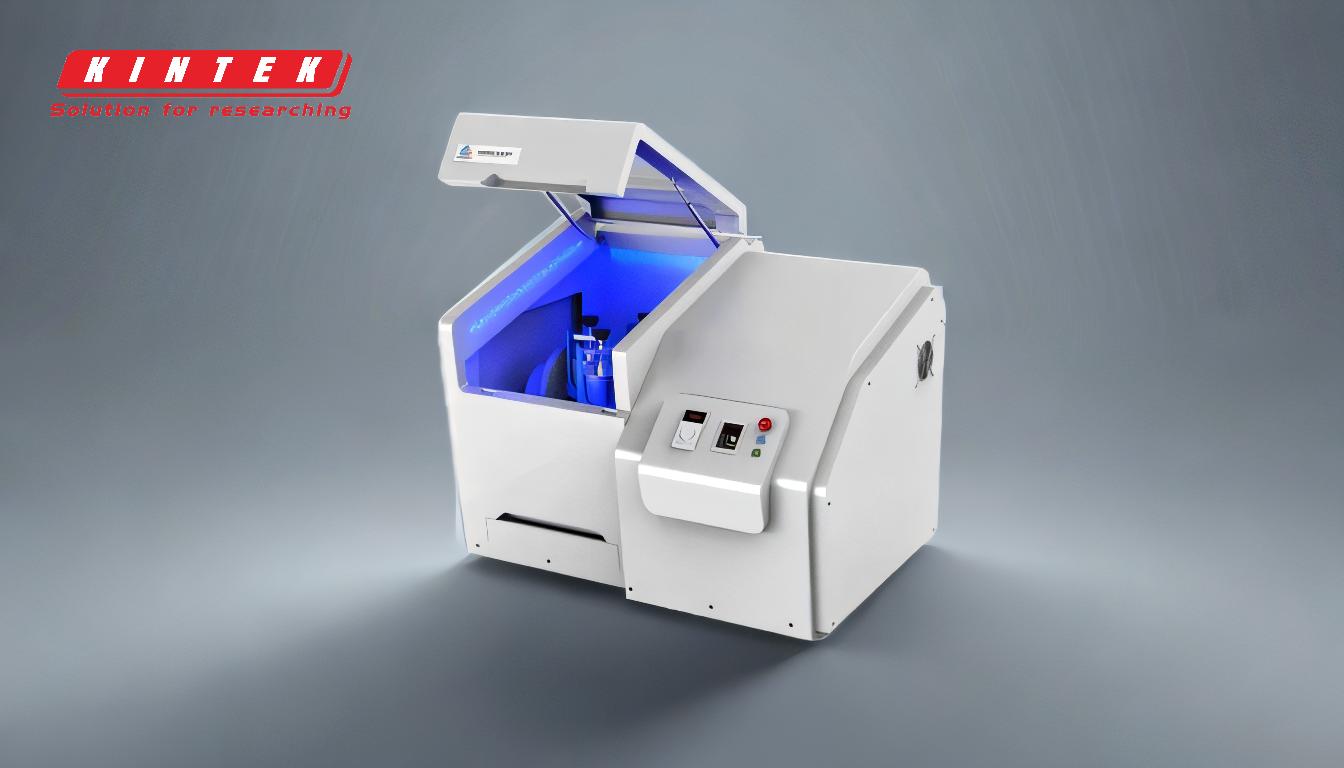
-
Ottimizzare la velocità di rotazione
- La velocità di rotazione del mulino a sfere influisce direttamente sull'efficienza di macinazione.
- Se la velocità è troppo bassa, le sfere non saranno sollevate abbastanza da creare un impatto significativo, riducendo l'efficienza di macinazione.
- Se la velocità è troppo alta, le sfere possono centrifugare, attaccandosi alle pareti del mulino e riducendo l'azione di macinazione.
- La velocità ottimale è in genere il 65-75% della velocità critica, dove per velocità critica si intende la velocità alla quale le sfere iniziano a centrifugare.
-
Selezionare il giusto mezzo di macinazione
- Le dimensioni, la densità e il numero di sfere influenzano in modo significativo le prestazioni di macinazione.
- Le sfere più piccole sono migliori per la macinazione fine, mentre quelle più grandi sono più efficaci per la macinazione grossolana.
- La densità delle sfere deve corrispondere al materiale da macinare; i materiali più densi richiedono sfere più dense.
- Assicurare un rapporto adeguato tra sfere e materiale per massimizzare l'impatto e ridurre al minimo l'usura.
-
Controllare il rapporto di riempimento
- Il rapporto di riempimento si riferisce alla percentuale del volume del mulino riempita con il mezzo di macinazione.
- Un rapporto di riempimento ottimale (in genere 30-40%) garantisce un'azione macinante sufficiente senza sovraccaricare il mulino.
- Un riempimento eccessivo può ridurre l'efficienza di macinazione, mentre un riempimento insufficiente può causare un impatto e un'usura insufficienti.
-
Regolare il rapporto L:D
- Il rapporto tra la lunghezza del tamburo (L) e il diametro (D) influisce sul tempo di permanenza del materiale nel mulino.
- Un rapporto L:D ottimale (1,56-1,64) garantisce una macinazione efficiente senza un eccessivo consumo di energia.
- Un tamburo più lungo aumenta il tempo di permanenza, a vantaggio della macinazione fine, ma può ridurre la produttività.
-
Gestire la velocità di alimentazione e le proprietà del materiale
- La velocità di alimentazione deve essere bilanciata con la capacità di macinazione del mulino.
- Un sovraccarico di materiale può ridurre l'efficienza di macinazione e aumentare il consumo energetico.
- Anche le proprietà fisico-chimiche del materiale di alimentazione (ad esempio, durezza, contenuto di umidità) influiscono sulle prestazioni di macinazione.Può essere necessario apportare modifiche in base alle caratteristiche del materiale.
-
Garantire la rimozione tempestiva del prodotto macinato
- Uno scarico efficiente del materiale macinato previene la macinazione eccessiva e garantisce una qualità costante del prodotto.
- Utilizzare meccanismi di scarico appropriati (ad esempio, scarico a griglia, scarico a sfioro) in base al materiale e alla finezza desiderata.
- Monitorare e regolare regolarmente il sistema di scarico per mantenere prestazioni ottimali.
-
Mantenere la forma della superficie del rivestimento
- La forma e le condizioni dell'armatura del mulino (rivestimento) influiscono sull'efficienza di macinazione e sull'usura.
- I rivestimenti lisci sono adatti per la macinazione fine, mentre quelli a coste o a onda sono più indicati per la macinazione grossolana.
- Ispezionare e sostituire regolarmente i rivestimenti usurati per mantenere l'efficienza della macinazione.
-
Monitoraggio e controllo della finezza di macinazione
- La finezza desiderata del prodotto macinato influenza i parametri di macinazione.
- Per particelle più fini, sono necessari tempi di macinazione più lunghi e sfere più piccole.
- Utilizzare l'analisi granulometrica per monitorare la finezza e regolare i parametri secondo necessità.
Intervenendo sistematicamente su questi fattori, è possibile aumentare in modo significativo la produzione e l'efficienza di un mulino a sfere.Ogni parametro deve essere attentamente ottimizzato in base al materiale specifico e ai requisiti operativi per ottenere i migliori risultati.
Tabella riassuntiva:
Fattore | Suggerimenti per l'ottimizzazione |
---|---|
Velocità di rotazione | Mantenere il 65-75% della velocità critica per un'efficienza di macinazione ottimale. |
Mezzo di macinazione | Utilizzare sfere più piccole per la macinazione fine, sfere più grandi per la macinazione grossolana.Adattare la densità delle sfere al materiale. |
Rapporto di riempimento | Mantenere un rapporto di riempimento del 30-40% per evitare un sovraccarico o un sotto-riempimento. |
Rapporto L:D | Ottimizzare il rapporto lunghezza/diametro del tamburo (1,56-1,64) per una macinazione efficiente. |
Velocità di alimentazione e materiale | Bilanciare la velocità di alimentazione con la capacità di macinazione; regolare la durezza e l'umidità del materiale. |
Rimozione del prodotto macinato | Utilizzare meccanismi di scarico appropriati per evitare un'eccessiva smerigliatura. |
Forma della superficie della corazza | Scegliere rivestimenti lisci per la macinazione fine, rivestimenti a coste/onde per la macinazione grossolana. |
Finezza di macinazione | Monitorare le dimensioni delle particelle e regolare i parametri di macinazione per ottenere la finezza desiderata. |
Siete pronti a ottimizzare la produzione del vostro mulino a sfere? Contattate i nostri esperti oggi stesso per soluzioni su misura!