L'aumento dell'efficienza del mulino a sfere comporta l'ottimizzazione di diversi fattori che influenzano le prestazioni di macinazione.Tra questi, le dimensioni del tamburo (diametro e lunghezza), il rapporto tra diametro e lunghezza del tamburo, le proprietà fisiche e chimiche del materiale di alimentazione, le dimensioni e il riempimento delle sfere di macinazione, la forma della superficie di armatura, la velocità di rotazione, la finezza di macinazione e la rimozione tempestiva del prodotto macinato.Inoltre, fattori quali il tempo di permanenza del materiale nel mulino, la velocità di alimentazione e la natura del materiale da macinare svolgono un ruolo cruciale.Regolando con attenzione questi parametri, l'efficienza del mulino a sfere può essere migliorata in modo significativo, con conseguente aumento della produttività e riduzione del consumo energetico.
Punti chiave spiegati:
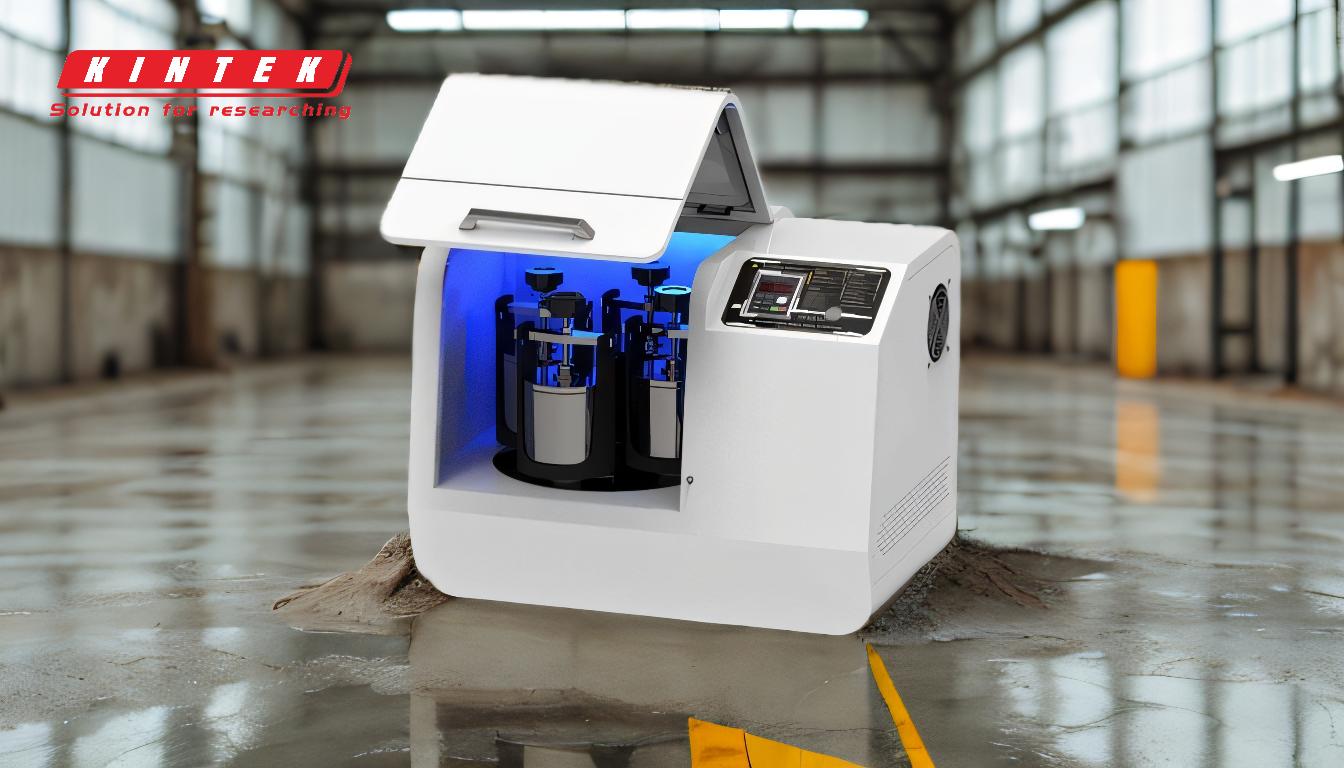
-
Ottimizzare le dimensioni del tamburo e il rapporto L:D:
- Diametro del tamburo:Diametri del tamburo più grandi possono aumentare la capacità e l'efficienza di macinazione del mulino.
- Rapporto lunghezza/diametro (L:D):Il rapporto L:D ottimale per i mulini a sfera è compreso tra 1,56 e 1,64.Questo rapporto assicura una macinazione efficiente fornendo il giusto equilibrio tra la lunghezza e il diametro del tamburo, che influisce sul tempo di permanenza del materiale e sull'azione di macinazione.
-
Regolazione del riempimento delle sfere e delle dimensioni:
- Riempimento delle sfere:La percentuale del volume del mulino riempito con sfere di macinazione (rapporto di riempimento) deve essere ottimizzata.Un riempimento eccessivo può portare a una macinazione inefficiente, mentre un riempimento insufficiente può ridurre l'azione macinante.
- Dimensioni delle sfere:L'utilizzo di un mix di sfere di diverse dimensioni può migliorare l'efficienza della macinazione.Le sfere più grandi sono efficaci per la macinazione grossolana, mentre quelle più piccole sono migliori per la macinazione fine.Una miscela bilanciata garantisce una macinazione efficace sia delle particelle grossolane che di quelle fini.
-
Controllo della velocità di rotazione:
- Velocità critica:La velocità di rotazione del mulino deve essere prossima alla velocità critica (la velocità alla quale le sfere iniziano a centrifugare).Il funzionamento alla giusta velocità garantisce che le sfere vadano in cascata e impattino il materiale in modo efficace, con conseguente migliore efficienza di macinazione.
- Velocità ottimale:La velocità ottimale si aggira solitamente intorno al 65-75% della velocità critica.Questo intervallo massimizza l'azione di macinazione senza causare un'usura eccessiva dei rivestimenti del mulino.
-
Gestione delle proprietà del materiale di alimentazione:
- Proprietà fisico-chimiche:La durezza, la densità e il contenuto di umidità del materiale di alimentazione possono influire sull'efficienza di macinazione.I materiali più morbidi si macinano più facilmente, mentre quelli più duri richiedono più energia.La regolazione della velocità di alimentazione e il pretrattamento del materiale (ad esempio, l'essiccazione) possono migliorare l'efficienza.
- Velocità di alimentazione e livello:Il mantenimento di una velocità e di un livello di alimentazione costanti nel mulino garantisce condizioni di macinazione costanti.Un sovraccarico del mulino può portare a una macinazione inefficiente, mentre un sottocarico può causare un'usura eccessiva delle sfere e dei rivestimenti.
-
Ottimizzare la finezza di macinazione e la rimozione del prodotto:
- Finezza di macinazione:La finezza desiderata del prodotto macinato deve essere bilanciata con l'efficienza di macinazione.Una macinazione eccessiva può comportare uno spreco di energia, mentre una macinazione insufficiente potrebbe non soddisfare le specifiche del prodotto.
- Rimozione tempestiva del prodotto macinato:Un'efficiente rimozione del prodotto macinato dal mulino impedisce una macinazione eccessiva e garantisce che il mulino funzioni alla capacità ottimale.Ciò può essere ottenuto utilizzando meccanismi di scarico appropriati (ad esempio, scarico a griglia, scarico a sfioro).
-
Considerare la forma della superficie dell'armatura e il design del rivestimento del mulino:
- Forma della superficie dell'armatura:La forma e il design dei rivestimenti del mulino (armatura) possono influenzare l'azione di macinazione.I rivestimenti lisci favoriscono l'effetto a cascata, mentre quelli nervati o con sollevatore favoriscono l'azione di sollevamento e caduta delle sfere, migliorando l'efficienza di macinazione.
- Materiale del rivestimento:Il materiale delle camicie deve essere scelto in base al tipo di materiale da macinare e alla resistenza all'usura desiderata.Per i materiali abrasivi si utilizzano spesso materiali più duri, come l'acciaio al manganese.
-
Monitoraggio e controllo del tempo di permanenza:
- Tempo di permanenza:Il tempo che il materiale trascorre nella camera del mulino influisce sul grado di macinazione.Tempi di permanenza più lunghi possono portare a una macinazione più fine, ma possono anche aumentare il consumo energetico.La regolazione della velocità di alimentazione e della velocità del mulino può aiutare a controllare il tempo di residenza.
-
Manutenzione e monitoraggio regolari:
- Usura e usura:L'ispezione e la manutenzione regolari del mulino, compresi i rivestimenti e le sfere di macinazione, possono evitare tempi di fermo imprevisti e mantenere l'efficienza di macinazione.
- Monitoraggio del processo:Il monitoraggio continuo del processo di macinazione, compresa la distribuzione delle dimensioni delle particelle e il consumo energetico, può aiutare a identificare le inefficienze e consentire aggiustamenti tempestivi.
Intervenendo sistematicamente su questi fattori chiave, è possibile aumentare significativamente l'efficienza di un mulino a sfere, con conseguente aumento della produttività, riduzione del consumo energetico e migliori prestazioni complessive.
Tabella riassuntiva:
Fattore chiave | Suggerimenti per l'ottimizzazione |
---|---|
Dimensioni del tamburo | - Un diametro maggiore del tamburo aumenta la capacità.Rapporto L:D ottimale: 1,56-1,64. |
Riempimento e dimensioni delle sfere | - Ottimizzare il rapporto di riempimento.Utilizzare un mix di dimensioni delle sfere per la macinazione grossolana e fine. |
Velocità di rotazione | - Operare al 65-75% della velocità critica per un'azione di macinazione ottimale. |
Proprietà del materiale di alimentazione | - Regolare la velocità di avanzamento e pretrattare i materiali in base a durezza, densità e umidità. |
Finezza di macinazione e rimozione | - Bilanciare la finezza con l'efficienza.Utilizzare meccanismi di scarico adeguati. |
Design della superficie e del rivestimento dell'armatura | - Usare rivestimenti con nervature o sollevatori per una migliore levigatura.Scegliere materiali di rivestimento durevoli. |
Tempo di permanenza | - Controllo con la velocità di avanzamento e la velocità del mulino per evitare una macinazione eccessiva. |
Manutenzione e monitoraggio | - Ispezionare regolarmente rivestimenti e sfere.Monitorare le dimensioni delle particelle e il consumo energetico. |
Siete pronti a ottimizzare l'efficienza del vostro mulino a sfere? Contattate i nostri esperti oggi stesso per soluzioni su misura!