La deposizione sputter è un processo critico nella produzione di semiconduttori, utilizzato per depositare pellicole sottili di materiali su substrati. Questo processo prevede il bombardamento di un materiale bersaglio con ioni ad alta energia, tipicamente provenienti da un plasma di argon, che fa sì che gli atomi del bersaglio vengano espulsi e depositati su un substrato. Questo metodo è particolarmente apprezzato per la sua capacità di produrre rivestimenti altamente puri e uniformi, essenziali per i requisiti ad alte prestazioni dei componenti dei semiconduttori. La deposizione sputter è versatile, capace di depositare un'ampia gamma di materiali, inclusi metalli e ceramiche, e si è evoluta in modo significativo dalla sua scoperta a metà del XIX secolo.
Punti chiave spiegati:
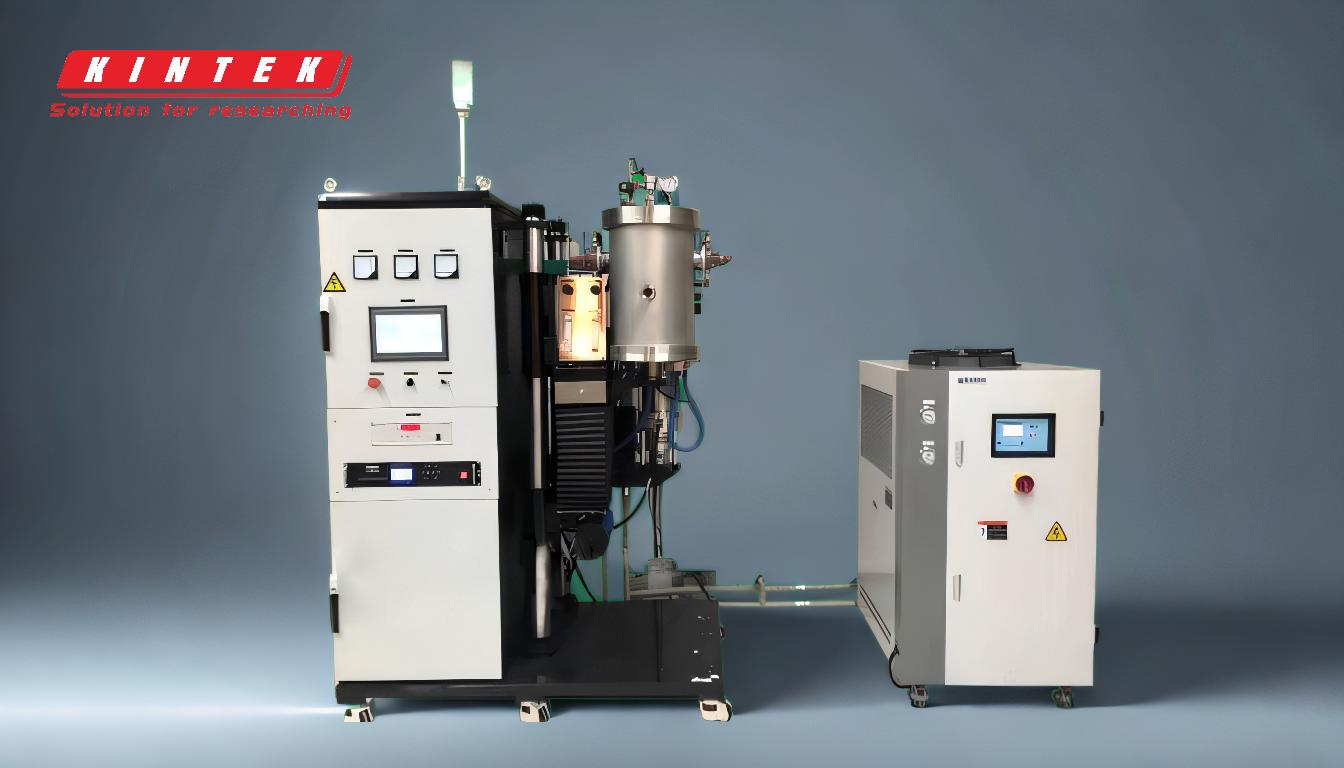
-
Meccanismo di deposizione dello sputter:
- La deposizione sputter funziona esponendo un materiale target a un plasma di ioni ad alta energia, solitamente argon. Questi ioni entrano in collisione con il bersaglio, provocando l'espulsione degli atomi dalla sua superficie.
- Gli atomi espulsi formano una nuvola di vapore che poi si condensa su un substrato, formando una pellicola sottile. Questo processo è altamente controllato per garantire uniformità e purezza del materiale depositato.
-
Applicazioni nella produzione di semiconduttori:
- Nella produzione di semiconduttori, la deposizione sputtering viene utilizzata per applicare film sottili di materiali come l'oro, essenziali per la loro eccellente conduttività elettrica e termica.
- Il processo è fondamentale per creare gli intricati strati di materiali metallici e dielettrici necessari nei circuiti integrati e in altri dispositivi a semiconduttore.
-
Sviluppo storico e progressi tecnologici:
- La deposizione di polverizzazione catodica fu osservata per la prima volta a metà del XIX secolo e trovò applicazioni commerciali negli anni '30.
- Dopo un periodo di declino negli anni '50, la tecnica riacquistò popolarità alla fine degli anni '50 e all'inizio degli anni '60 grazie ai progressi nella tecnologia del vuoto e allo sviluppo dello sputtering a radiofrequenza (RF), che consentiva la deposizione di materiali dielettrici.
-
Importanza della purezza negli obiettivi di sputtering:
- La purezza del target dello sputtering è fondamentale, soprattutto nelle applicazioni dei semiconduttori. Anche le tracce di impurità possono influenzare significativamente le prestazioni dei componenti dei semiconduttori.
- Obiettivi di elevata purezza garantiscono che i film depositati abbiano le proprietà elettriche e termiche necessarie per i dispositivi a semiconduttore ad alte prestazioni.
-
Utilizzo nella microscopia elettronica a scansione (SEM):
- Il rivestimento Sputter viene utilizzato anche nel SEM per migliorare l'imaging dei campioni. Depositando un sottile strato conduttivo su campioni non conduttivi o sensibili al raggio, riduce gli effetti di carica e migliora il rapporto segnale-rumore, ottenendo immagini più chiare e dettagliate.
La deposizione sputter rimane una tecnica fondamentale nella fabbricazione di moderni dispositivi a semiconduttore, offrendo precisione e versatilità che non hanno eguali rispetto ad altri metodi di deposizione. La sua continua evoluzione e adattamento a nuovi materiali e tecnologie sottolineano la sua importanza nel progresso della produzione di semiconduttori.
Tabella riassuntiva:
Aspetto chiave | Dettagli |
---|---|
Meccanismo | Gli ioni di argon ad alta energia bombardano un bersaglio, espellendo gli atomi per formare una pellicola sottile. |
Applicazioni | Utilizzato in dispositivi a semiconduttore per conduttività elettrica e termica. |
Sviluppo storico | Scoperto nel XIX secolo; avanzato con lo sputtering RF negli anni '60. |
Purezza dell'obiettivo | Gli obiettivi di elevata purezza garantiscono proprietà elettriche e termiche ottimali. |
Applicazioni SEM | Migliora l'imaging depositando strati conduttivi su campioni non conduttivi. |
Scopri come la deposizione sputtering può rivoluzionare i tuoi processi relativi ai semiconduttori— contatta i nostri esperti oggi stesso !